di Marco de’ Francesco ♦ Le strategie della storica azienda di Molteno, parte del gruppo MLF (110 milioni di fatturato) esempio classico di impresa del Quarto Capitalismo. Enpower, che permette la customizzazione e Epc contractor con la realizzazione di macchine plug and play. La partnership con Siemens
Due strategie di crescita per la Mario Frigerio, storica azienda di macchine per la lavorazione di fili, funi e cavi di acciaio, rame ed alluminio. La prima, di tipo industriale, si chiama Empower, e comporta la produzione di lotti standard a magazzino, che associati con diverse combinazioni consentono di realizzare macchine differenti. Si tratta di venire incontro alle variabili di configurazione richieste dai clienti. La seconda è consiste in un approccio “olistico”. L’azienda, che è l’unica al mondo a produrre impianti che svolgono tutte le lavorazioni tipiche del settore (trafilatura, estrusione, viplatura e cordatura), intende proporsi come EPC contractor (Engineering, Procurement and Construction), e cioè come una società che non si occupa solo della realizzazione materiale della macchina, ma anche dei servizi che riguardano tutte le attività di gestione di un cantiere dalll’installazione alla messa in servizio.
La Mario Frigerio è espressione del Quarto Capitalismo, categoria di imprese di medie dimensioni che riescono ad associare flessibilità e proiezione globale. L’azienda di Molteno (Lecco) è attualmente parte del gruppo MFL, che si è sviluppato attorno alla prima e che, nel 2018, ha raggiunto un fatturato di circa 100 milioni. Punta molto sulla tecnologia, ad esempio con un progetto per automatizzare il controllo di qualità grazie al machine learning. D’altra parte, da anni ha stretto una partnership con Siemens, il colosso dell’automazione, e non solo. Ne abbiamo parlato con Lucia Frigerio, vice presidente del gruppo.
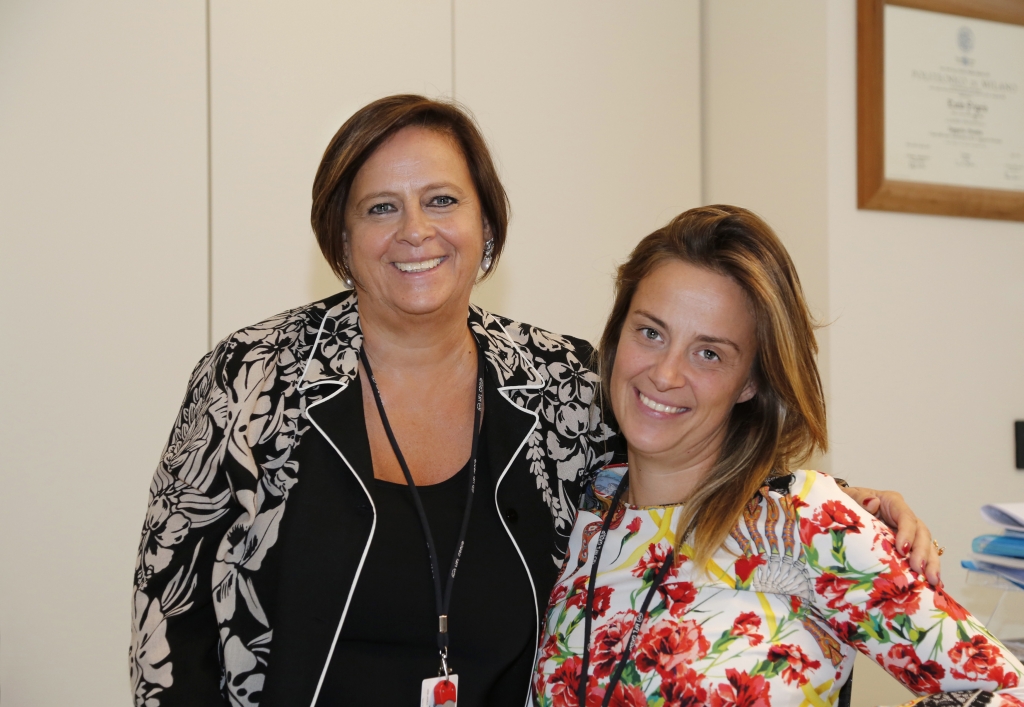
Dalle macchine per il pane a quelle per i cavi d’acciaio
La Mario Frigerio Spa nasce a Lecco nel 1897, come piccola officina per la realizzazione di macchine per il pane. Questa attività durerà per oltre mezzo secolo, finché, nel dopoguerra, l’azienda non acquisterà un brevetto per produrre macchine per la trafilatura dell’acciaio. A questo impiego si aggiungeranno, nel 1997, i macchinari per la lavorazione di fili di rame e di alluminio. Ma il cambiamento vero e proprio si ha con la crisi economica del 2008, che comporta il fallimento di tante aziende della zona. Due anni dopo, infatti, iniziano le acquisizioni; inoltre, nello stesso periodo, lavoratori con esperienza si aggiungono al team dell’azienda, portando nuove competenze. Nel frattempo, la società fonda una nuova azienda ad Ascoli Piceno e si struttura nel gruppo MFL, attualmente composto da quattro aziende – Mario Frigerio Spa, Fridea Srl, la catalana Construcciones Mecánicas Caballé e la cinese Nantong Frigerio Machinery.
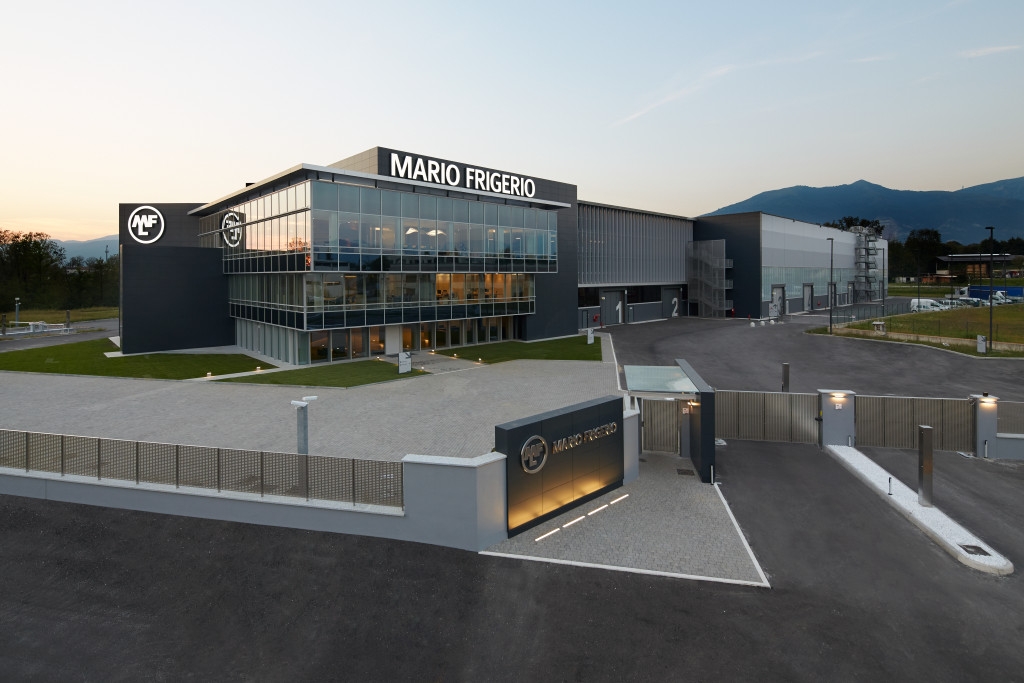
Il gruppo ha una struttura finanziaria, la holding milanese Semplice Spa; ma gli headquarter e il più importante stabilimento si trovano a Molteno, in provincia di Lecco, dove la Mario Frigerio si era trasferita nel 2014. MFL ha più di 300 dipendenti, di cui 77 ingegneri; punta sulle esportazioni, che nel 2018 hanno raggiunto una quota record di circa il 98% rispetto al fatturato. Più membri della famiglia della vice presidente Lucia Frigerio hanno avuto o hanno un ruolo in azienda: il bisnonno, e cioè il fondatore Mario; il nonno Camillo; il padre Marco; la madre Emilia Tentori, attuale amministratore delegato; e lo zio Mario, attuale presidente. La storia è quella tipica di realtà industriali del Nord Italia che si sono sviluppate attorno al nucleo familiare. «Io stessa – concede Lucia Frigerio – sono vissuta in azienda fin da piccola, I compiti venivo a farli in fabbrica, da mio padre».
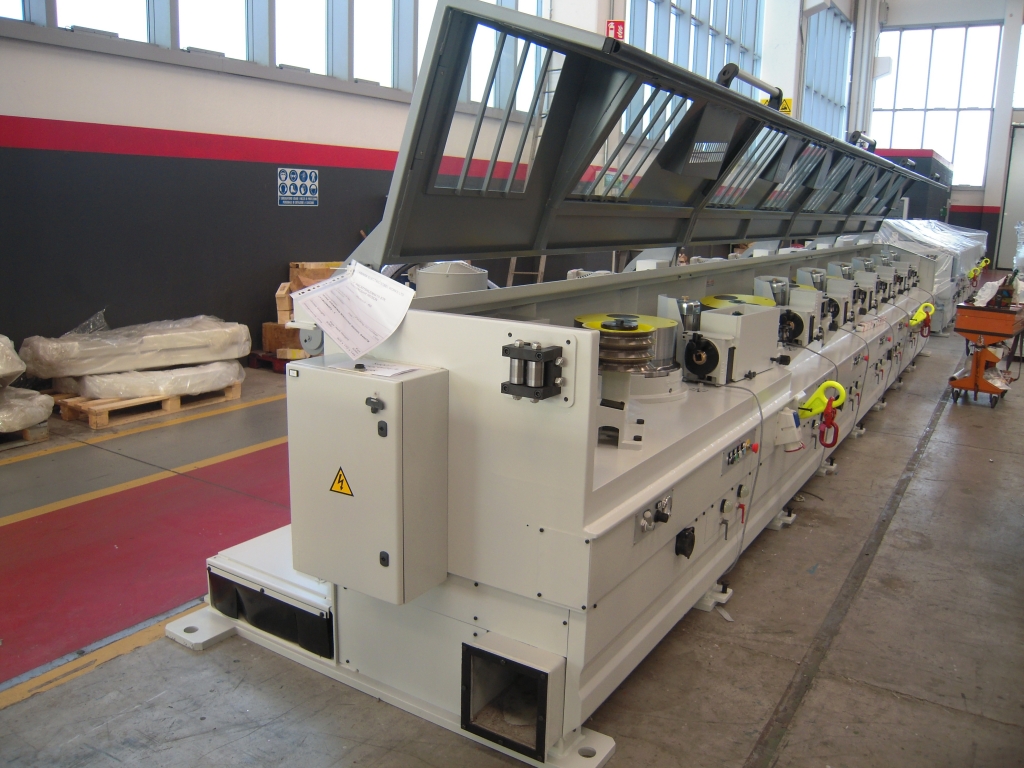
La strategia “Empower”
«Non c’è modo di fermare l’escalation della complessità del prodotto!» – dicono in MFL Group. Ed è vero. La corsa alla personalizzazione delle macchine, a una estrema configurazione, è inarrestabile in più settori della manifattura. Dietro, c’è la richiesta dell’azienda-cliente di fare più cose, e di realizzarle in modo diverso in base alle necessità dell’utente finale o delle specifiche di un progetto determinato. Solo che si è scoperto che ogni volta che il numero delle varianti è raddoppiato, i relativi costi sono aumentati dal 20% al 30%. Bisognava definire una strategia industriale per garantire la differenziazione del prodotto a costi accettabili, per assicurare la redditività nonostante, peraltro, le pressioni sui tempi di consegna e il trend che per altre aziende descrive una costante diminuzione della marginalità. Per MFL Group la tattica ha un nome: Empower.
Secondo la Frigerio «con questo mio progetto siamo riusciti ad eliminare le inefficienze, a “guadagnare” un mese e mezzo di fatturato e a ridurre il lead-time (tempo di attraversamento) da sei mesi a cinque». Ma come funziona? Con un paragone un po’ irrituale, si considerino i mattoncini delle costruzioni per gioco. Ce ne sono di diverse forme e dimensioni. Assemblandoli in modo diverso, si può dar vita ad un castello o ad una nave. «Noi lavoriamo in magazzino moduli standard, che associati con diverse combinazioni consentono la realizzazione di macchine differenti. I “codici” sono moltiplicati, e con questo sistema è aumentata molto la flessibilità della progettazione».
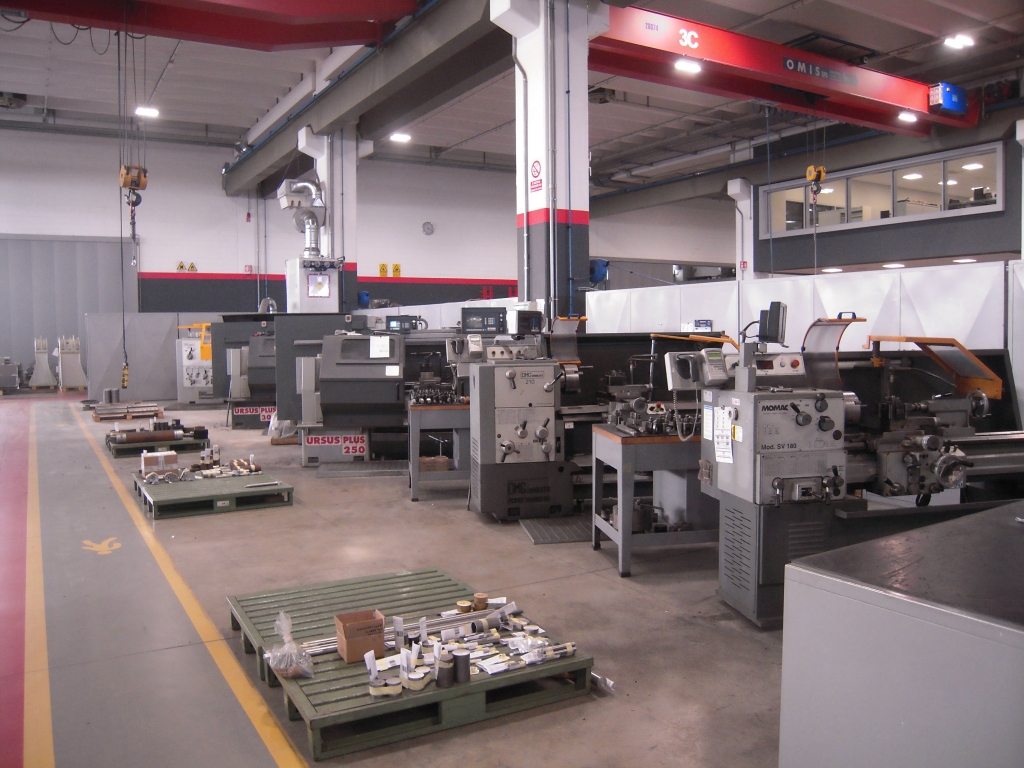
Si potrebbe pensare ad un magazzino ridondante. «No, in realtà acquistiamo materiale a scorta minima, per l’occorrenza». Sono diminuiti anche i tempi di montaggio. «In misura notevole, direi». Questa strategia industriale, Empower, in un certo senso “anticipa” la richiesta di personalizzazione del cliente. È il modello “configure-to-order”. Implica la riduzione del contenuto personalizzato a favore di un aumento di quello standard diversamente configurabile. Ha un vantaggio intrinseco: il rischio di guasti dovuti a modifiche non documentate diminuisce drasticamente. Funzionale a Empower è stato il raggruppamento, nel 2014, degli stabilimenti. «Erano cinque, ora in zona ce n’è uno con più spazio. L’unificazione ha comportato il miglioramento dei processi».
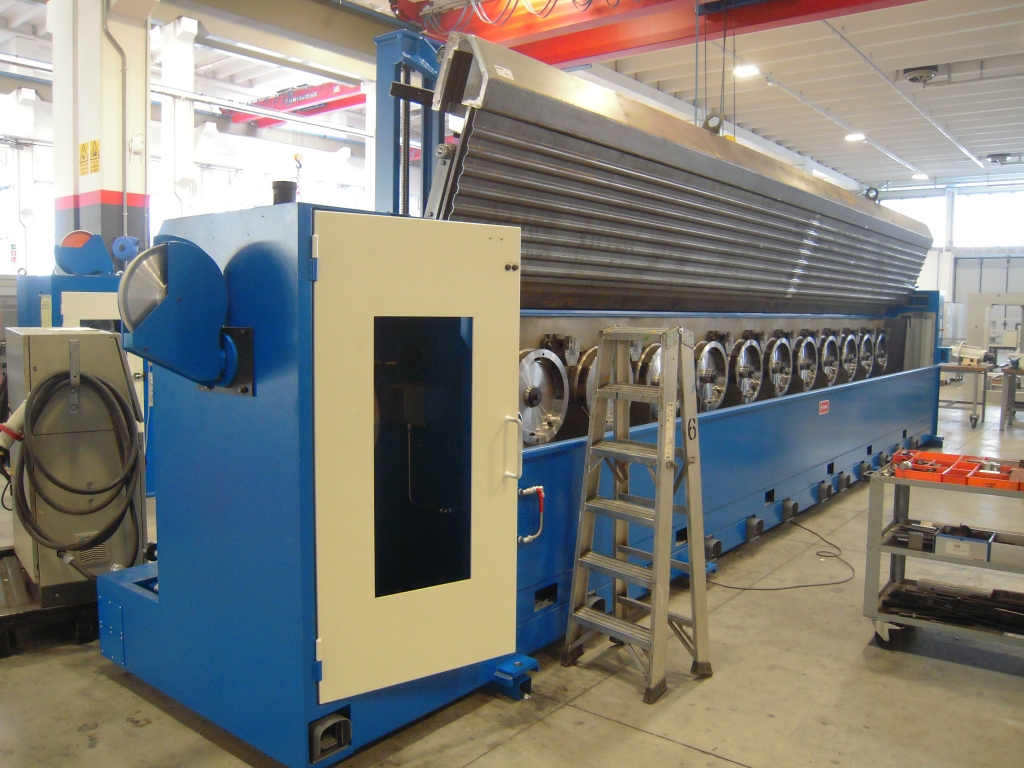
L’evoluzione della strategia olistica: verso l’Epc
«Siamo gli unici al mondo a fare tutto» – afferma la Frigerio. Il gruppo, cioè, è l’unico al mondo ad occuparsi di trafilatura, estrusione e cordatura al contempo, sia per l’acciaio che per l’alluminio e per il rame. Altre realtà, anche più grandi, hanno finito per specializzarsi in questa o quella attività. Secondo la Frigerio, questa caratteristica avrebbe favorito l’internazionalizzazione del gruppo, iniziata nel 1995 e che oggi ha assunto dimensioni che si riscontrano nelle già accennate percentuali di quota export sul fatturato. Ora, però, anche per espandersi ulteriormente all’estero, il gruppo ha deciso di cambiare passo. «Il prossimo step è presentarsi come Epc contractor» – afferma la Frigerio. Epc sta per “engineering, procurement and construction”, ed è una forma particolare di accordo contrattuale. Con essa il gruppo non si obbliga solo alla progettazione e alla costruzione della macchina, ma anche all’intera gestione del cantiere in fase di avviamento delle linee. «Dobbiamo puntare a realizzare macchine plug and play e presentarci come società di ingegneria a supporto di tutte le attività negli stabilimenti dei nostri clienti».
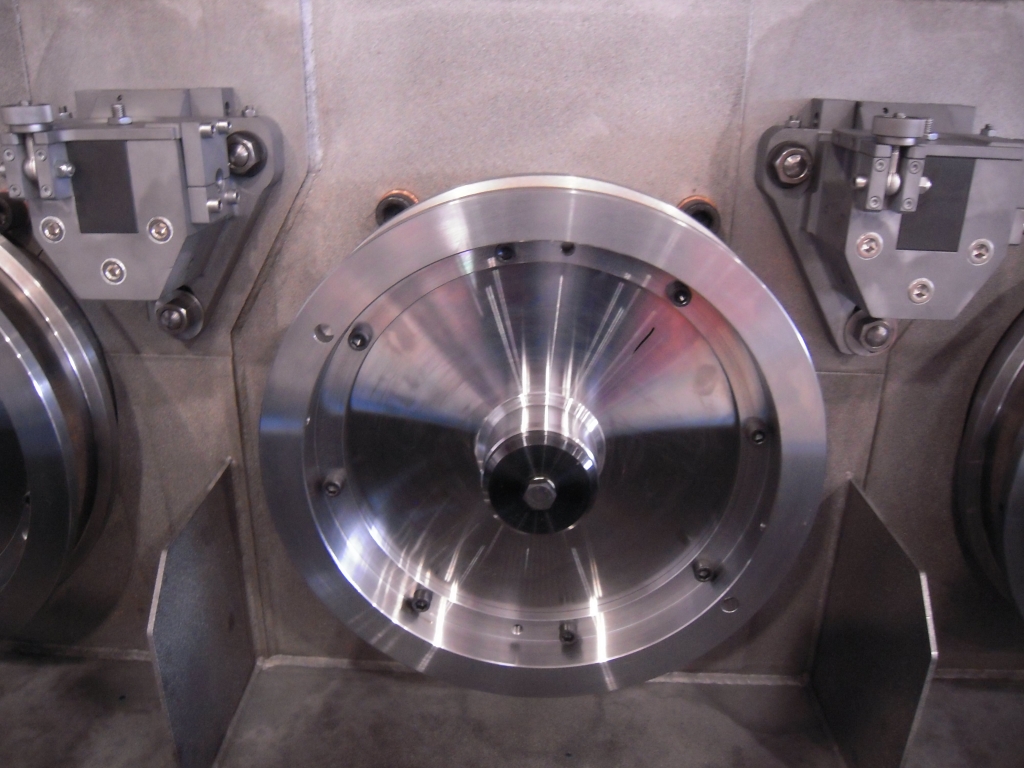
Il futuro prossimo del controllo di qualità
«Per noi la ricerca e sviluppo è attività quotidiana: le commesse richiedono avanzamenti incrementali e talvolta veri e propri salti di qualità tecnologici» – afferma la Frigerio. L’azienda ha sviluppato innovazioni proprie. Si pensi al decapaggio. Si tratta di un’operazione chimica effettuata per eliminare strati superficiali di un materiale tramite soluzioni di acido od alcali. Le vergelle di acciaio tendono ad arrugginire. Così, prima di lavorarle, normalmente vanno “pulite”. Solo che per la trafilatura il problema dello smaltimento di sostanze chimiche non è da poco; così, in azienda hanno inventato un decapaggio meccanico, che si ottiene grazie all’azione di tele abrasive.
E poi c’è una grossa novità in arrivo. «Due ingegneri (con PhD dell’Università Politecnica delle Marche) stanno sviluppando una soluzione di machine learning (il cosiddetto apprendimento automatico, un insieme di metodi statistici utilizzati per migliorare progressivamente la performance di un algoritmo nell’identificare pattern nei dati) per il controllo di qualità di cavi di plastica. L’algoritmo è basato su reti neurali, un modello matematico composto da tanti neuroni artificiali, che per certi versi replicano il funzionamento di quelli biologici, e cioè delle piccole componenti del cervello che ci consentono di ragionare. Ora siamo in fase di acquisizione dati, poi offriremo un “pacchetto” come servizio sulla macchina».
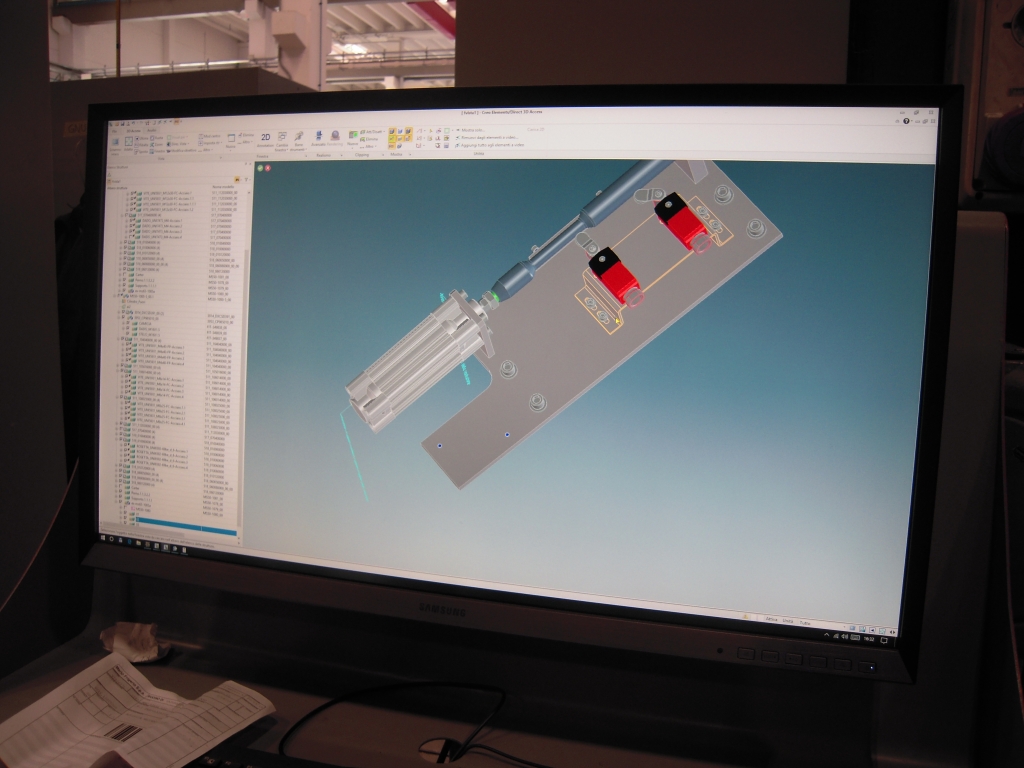
Il rapporto con Siemens
La relazione con il gigante dell’automazione Siemens è molto intenso. Peraltro la Mario Frigerio Spa è tra i soci fondatori dell’Associazione MindSphere World, della quale Lucia Frigerio è vice-presidente e tesoriere del consiglio direttivo. L’associazione romuove MindSphere, una piattaforma (software più servizi) basata su Cloud per la raccolta e l’analisi dei dati relativi alla produzione che consente di utilizzare delle “app” dedicate all’ottimizzazione degli asset e dei processi. Industria Italiana se ne è occupata più volte, ad esempio qui. Per la Frigerio «è una collaborazione, quella con Siemens, che dura da molto tempo. Non si tratta solo di comprare hardware e software. Siemens, che ha un enorme quantità di prodotti installati, conosce best practice in tutto il mondo e in settori diversi dal nostro, come il packaging; alcune novità e competenze relative ad altri comparti possono essere “riversate” nel nostro». In effetti secondo Giuliano Busetto, che guida l’ Operating Company Digital Industries di Siemens Italia, «l’azienda è tra le prime ad essere informate di qualsiasi novità tecnologica».
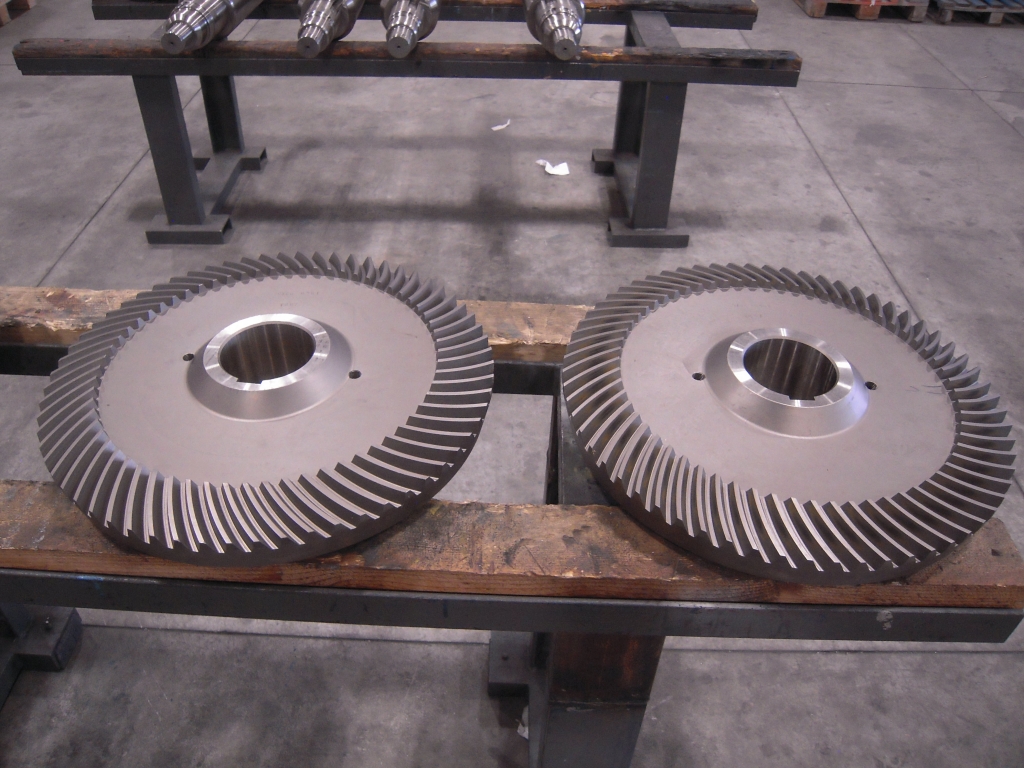
Viaggio in azienda
L’esplorazione della Mario Frigerio è di particolare interesse per Industria Italiana. Infatti l’azienda non si limita al montaggio di pezzi prodotti altrove. «Diversamente dai competitor, noi abbiamo tutto il reparto di 13 macchine utensili dedicate alla lavorazione delle componenti degli impianti» – afferma la Frigerio. Lo stabilimento è molto vasto, ricoprendo un’area pari a 30mila metri quadrati, e quindi più o meno come tre campi da calcio. Da qui escono ogni giorno tre container da 20 tonnellate. Quante macchine? Dipende dalle dimensioni. Ce ne sono di molto grandi; e anche i componenti sono talora molto pesanti. Infatti il soffitto dell’azienda è percorso da carri ponte, per i trasporti intralogistici.
La prima tappa è una grande alesatrice, e cioè una macchina per correggere l’assialità e il diametro dei fori. Può lavorare pezzi fino a dieci metri. Ci sono anche torni e frese, per il controllo utensili. A proposito di controllo, l’azienda è certificata Iso 9001 (standard gestione di qualità), 14001 (gestione ambientale) e 18001 (sicurezza). La Mario Frigerio realizza in proprio anche gli ingranaggi per i riduttori, circostanza che comporta risparmi sui costi. Nell’area di montaggio ci sono macchine per la trafilatura, alcune non ancora complete. «La trafilatura del rame avviene in immersione, quella dell’acciaio a secco».
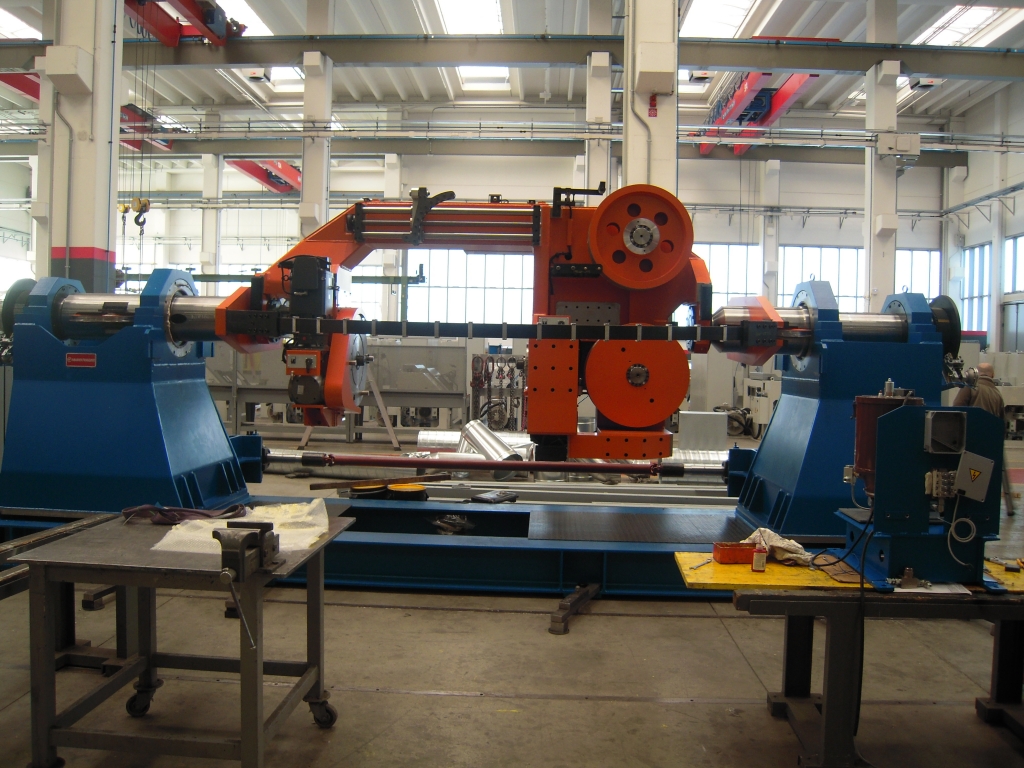
Ma capita mai che il filo si rompa? «È quello che si deve evitare». Segue un impianto importante, adibito alla realizzazione di particolari funi d’acciaio utilizzate nel mondo del precompresso per la costruzione di ponti e in generale per l’edilizia. Altra tappa importante è l’area di collaudo. È qui che si può notare una macchina completa per la trafilatura dell’acciaio. Costa circa 400mila euro. «È il risultato della strategia Empower. Con la combinazione dei componenti, possiamo coprire il parco macchine della trafilatura». Segue l’area dedicata al trasporto. Un ultimo appunto che mostra l’evoluzione tecnologica anche nelle fasi di montaggio. La Mario Frigerio è paperless: l’operatore, per montare il pezzo, ha a disposizione su monitor un sistema 3D, che gli indica come procedere con esattezza, pensionando i vecchi disegni a due dimensioni.