di Marco de’ Francesco ♦ E’ già attiva nel Polo Meccatronica un’area a disposizione delle aziende con tutti i macchinari destinati a ridurre il time to market dalla progettazione alla realizzazione. Una soluzione pubblica a problemi privati, un centro per la ricerca, la sperimentazione e lo sviluppo di prodotti innovativi con l’obiettivo di ottimizzare il valore velocità nella produzione manifatturiera
Non è solo una questione di stare al passo con i tempi. È che il mercato è cambiato; è che le regole sono altre rispetto a quelle che vigevano poco tempo fa. L’azienda manifatturiera deve realizzare prodotti migliori, più innovativi ed efficienti e pronti per il mercato in tempi più rapidi. Si assiste, per esempio, ad una riduzione continua del time-to-market. «L’emergere di articoli nuovi e sempre più perfezionati, l’estensione e l’espansione delle linee, le continue revisioni e i costanti miglioramenti, creano ulteriori pressioni sulle aziende per mantenere un flusso costante di nuovi prodotti sul mercato. È assodato che qualsiasi ritardo di questo flusso determina perdite di profitto sempre più consistenti» – si legge in un saggio (Nosa. F. O. Evbuomwan, “Design for time to market”).
La velocità è un fattore che influenza largamente le performance di una azienda manifatturiera. Si avverte la necessità di disegnare prodotti che possano essere liberati sul mercato in anticipo rispetto alla concorrenza; e che presentino contenuti tecnologici sempre più ricchi, sempre più intelligenti, per fare la differenza. Si innesca qui tutto il tema dell’Industry 4.0, osservato dal punto di vista della meccanica: additive manufacturing, cloud, big data, sensori, sicurezza e altro. Quelli che il mercato sta disegnando e sui quali l’azienda deve confrontarsi sono percorsi complessi. Ed è per questo che è nato il Polo Meccatronica di Rovereto. È il luogo dove nasce l’impresa intelligente, dicono a Rovereto. Ed è quello dove sono messi a disposizione delle aziende laboratori avanzati che le supportano nello sviluppo del prodotto. Il Trentino si è giocato la carta di lasciare alle aziende la possibilità di fruire del proprio patrimonio tecnologico dei centri di ricerca locale. Il cuore del Polo è il “Mechatronics Prototyping Facility”. Che qualche giorno fa ha svelato i propri segreti. Come funziona?
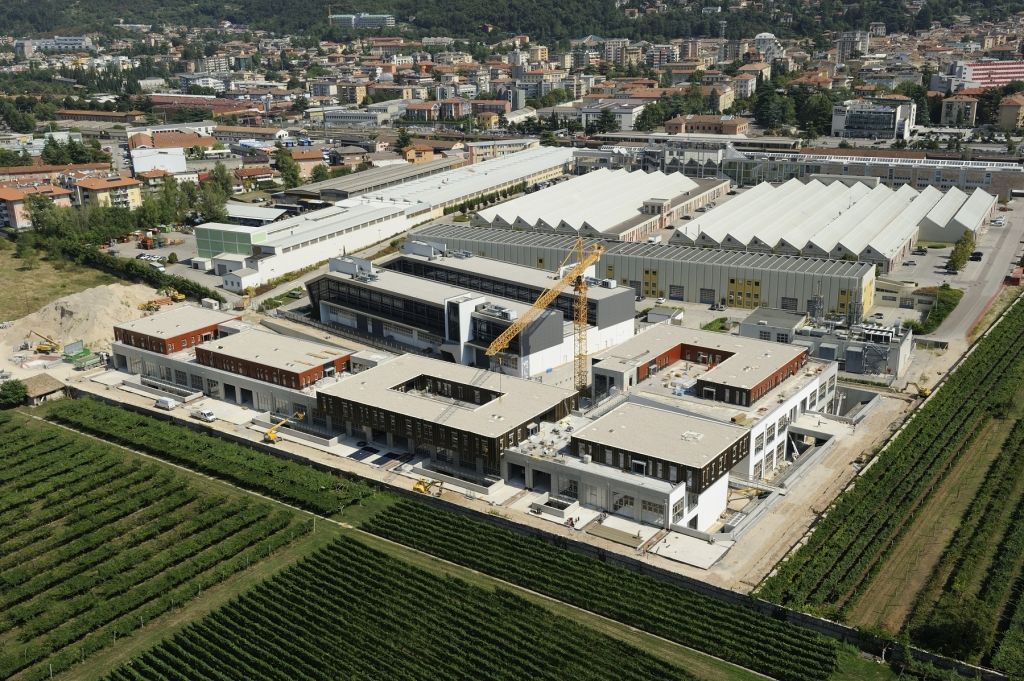
Il Polo Meccatronico di Rovereto
Un passo indietro. Qualche mese fa Industria Italiana aveva divulgato il caso del Polo di Rovereto. Si erano descritti sia il progetto che gli attori. Perché le cose stanno così: la Provincia autonoma di Trento ha deciso di investire complessivamente circa 85 milioni di euro. Per un piano che coinvolge non solo il “braccio operativo” Trentino Sviluppo, ma anche le locali università e associazione degli industriali; e poi la “Fondazione Bruno Kessler”, l’istituto tecnico tecnologico “G. Marconi” e il centro di formazione professionale “G. Veronesi” di Rovereto; e infine l’acceleratore privato “Industrio Ventures” e il Comune di Rovereto. Insieme per dare vita ad un luogo fisico dove le idee corrono veloci.
Al via ProM Facility
Ora c’è una novità nel crono-programma: ProM, il laboratorio per la ricerca e la prototipazione, costato 5 milioni di euro, è operativo già dai primi mesi del 2017. Quanto agli spazi, il Polo mette a disposizione 13mila metri quadrati per l’area produttiva (due corpi su due livelli e di edifici con struttura portante in legno) e 4mila per gli uffici. Circa 35mila metri quadrati sono quelli destinati al potenziamento dell’area industriale (in pratica, per le aziende che si insedieranno; ndr), mentre 25mila sono riservati al polo scolastico. ProM occupa un’area di 1.500 metri quadrati.
Ma veniamo alla visita al ProM Facility, definito come «un centro di innovazione per ricercare, sperimentare, sviluppare prodotti innovativi, in grado di combinare la meccanica tradizionale con i più moderni controlli elettronici, sensori e sistemi di prototipazione virtuale». Nel ProM si concentrano macchinari d’avanguardia: «tra i tanti a disposizione – afferma l’azienda – si segnalano stampanti 3D metalliche e polimeriche, una macchina taglio laser combinata per tubi e lamiere di diversi materiali, scanner 3D, un centro di fresatura in grado di combinare lavorazioni additive e sottrattive, una linea di prototipazione semi-automatica di schede elettroniche, un manipolatore per robotica cooperativa, un banco prove motori e un supercomputer per addestramento reti neurali profonde e altro ancora». Il giorno della visita erano presenti i tre progettisti: il direttore Paolo Gregori, il responsabile scientifico Paolo Bosetti e il referente tecnico Amos Collini, già responsabile dei laboratori di test presso Fondazione Bruno Kessler. Il ricercatore Marco Roveri, sempre di FBK (Fondazione Bruno Kessler), ha invece il compito specifico di sviluppare i servizi ICT per l’industria integrati con i servizi di prototipazione meccanica ed elettronica.
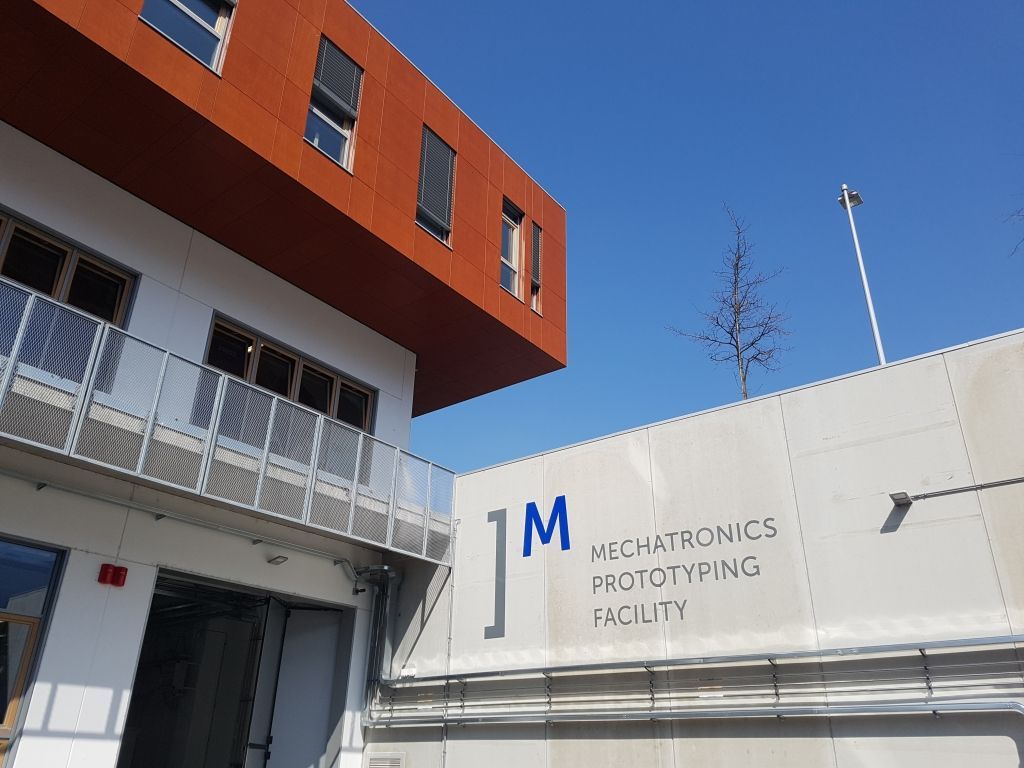
Non solo servizi ma crazione di competenze
Per Gregori «il laboratorio non offre solo servizi a prezzi di mercato alle aziende insediate in Polo Meccatronica o esterne: infatti ha stretto un accordo con Fondazione Bruno Kessler e Università di Trento per supportare, tra l’altro, due borse di dottorato all’anno. In questo modo si realizzerà uno degli scopi della mission, che è avvicinare i ricercatori all’impresa, con la possibilità di creare nuovi posti di lavoro ad alta specializzazione su esigenze direttamente stimolate dalle aziende. Gli spazi e i macchinari saranno anche a disposizione di stage e alternanze scuola-lavoro, così come le aziende potranno, anche grazie alla partecipazione diretta di Confindustria Trento, trovare occasioni di “training on the job” utili a formare nuove competenze interne. Al tempo stesso FBK metterà a disposizione le competenze di ricercatori o tecnologi che popoleranno questa Facility in cui le idee diventano realtà».
Time to market: la sfida contro il tempo
Bosetti ha ricordato che «io, Gregori e Collini siamo stati incaricati di progettare la facility nell’estate del 2015. La filosofia era quella di realizzare qualcosa che potesse aiutare le aziende ad avere accesso alle tecnologie recenti, assorbendo, in un certo senso, il rischio di impresa. Si pensi alle stampanti 3D: ora disponiamo di tre esemplari, uno dei quali costa 1,2 milioni di euro. In una sintesi netta, la questione era quella di trovare una soluzione pubblica a problemi privati». Si è già accennato al problema della prototipazione. «Il fatto è che il time-to-market (o TTM: il tempo che intercorre dall’ideazione di un prodotto alla sua effettiva commercializzazione; ndr) – ha continuato Bosetti – si è compresso: si assiste ad una sua continua riduzione. Nelle auto, ormai, si arriva sul mercato a due anni dal progetto. Così, la prototipazione assorbe una parte consistente del costo del prodotto finale. Incide sulla marginalità».
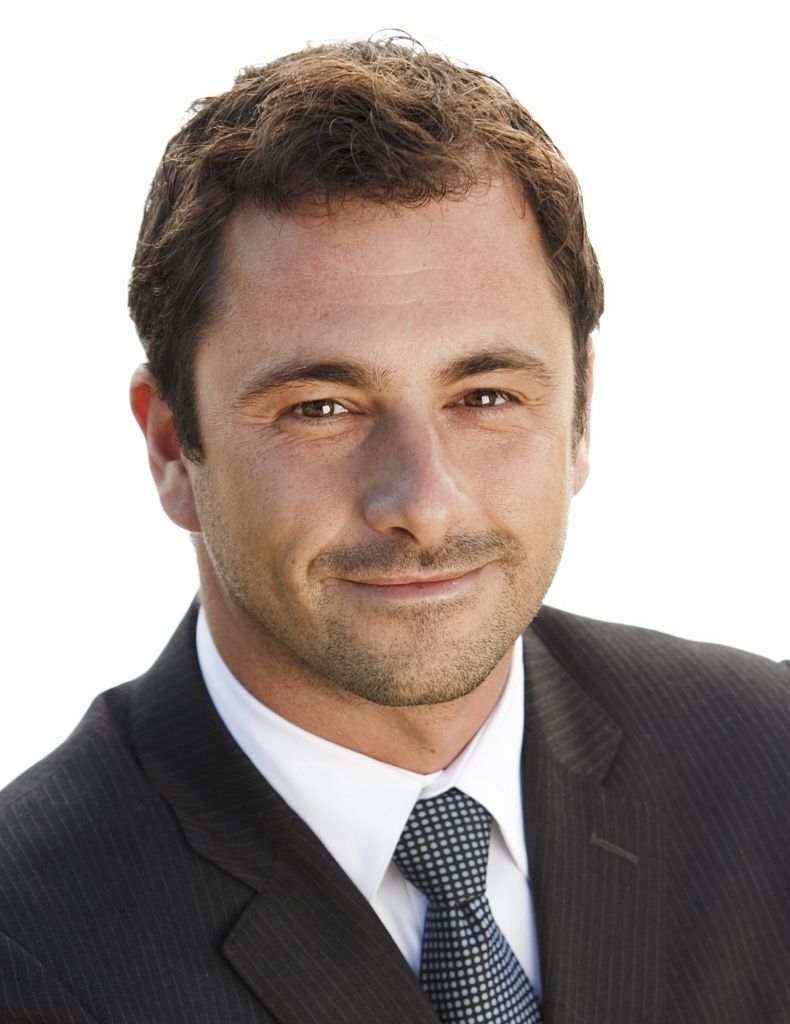
La prototipazione
Un laboratorio con gli strumenti adatti per ridurre i tempi può essere un fattore vincente, in quanto potenzialmente produttivo di un forte risparmio economico per l’azienda. «La Facility – ha chiarito Bosetti – è stata inaugurata il 3 aprile del 2015. Abbiamo speso già metà del budget a disposizione. Quattro le linee operative: anzitutto, la prototipazione “pura e semplice”, e cioè quella che riguarda le componenti metalliche e polimeriche, le schede elettroniche e altro; poi, il software, anche a supporto della cyber security. La sicurezza è molto importante, perché non riguarda solo il Pc. Si pensi alle automobili che si governano da sole; potrebbero essere dirottate in corsa. E poi, c’è tutto il tema della sicurezza nella produzione industriale. Ancora, c’è tutta la questione delle reti neurali profonde: qui ci sarà un server speciale, un supercalcolatore NVIDIA®DGX-1, per addestrare le reti in campo meccatronico».
Il supercomputer
Secondo l’azienda produttrice il supercomputer è «il primo sistema al mondo specifico per il deep learning e per l’analisi basata su AI: garantisce prestazioni pari a 250 server tradizionali. La soluzione è totalmente integrata con hardware, software di deep learning, strumenti di sviluppo e permette di eseguire le più usate applicazioni di analisi accelerata». In pratica serve a «ridurre i tempi di elaborazione dei dati, visualizzare più dati, accelerare i framework di deep learning e progettare reti neurali più sofisticate». Bosetti ha fatto l’esempio dei parametri dei processi industriali: «Invece dell’esperienza del lavoratore, c’è una rete neurale che definisce quali settaggi applicare».
C’è poi tutta la linea di testing. «Riguarda anche le schede elettroniche – ha continuato Bosetti – visto che devono superare prove di vario genere». In buona sostanza, Bosetti l’ha messa così: «Offriamo servizi, partnership e supporto al sistema formativo». Nella Facility sono presenti quattro tecnici. Peraltro, secondo il Polo, «i sistemi e i macchinari innovativi disponibili nella Pro-M Facility offrono alle aziende: supporto per la progettazione di tutti i livelli che concorrono alla realizzazione del sistema elettromeccanico e meccatronico: dall’interfaccia utente all’architettura hardware e software, fino ai modelli che ne descrivono il comportamento; la generazione automatica di casi di test, la verifica di proprietà temporali e la produzione di scenari di esecuzione in grado di evidenziare la presenza di difetti prima della consegna del prodotto al cliente finale; strumenti per misurare e valutare l’affidabilità di un sistema con tecniche automatiche di analisi e progettazione di sistemi di rilevamento, identificazione e recupero da guasti; e altro».
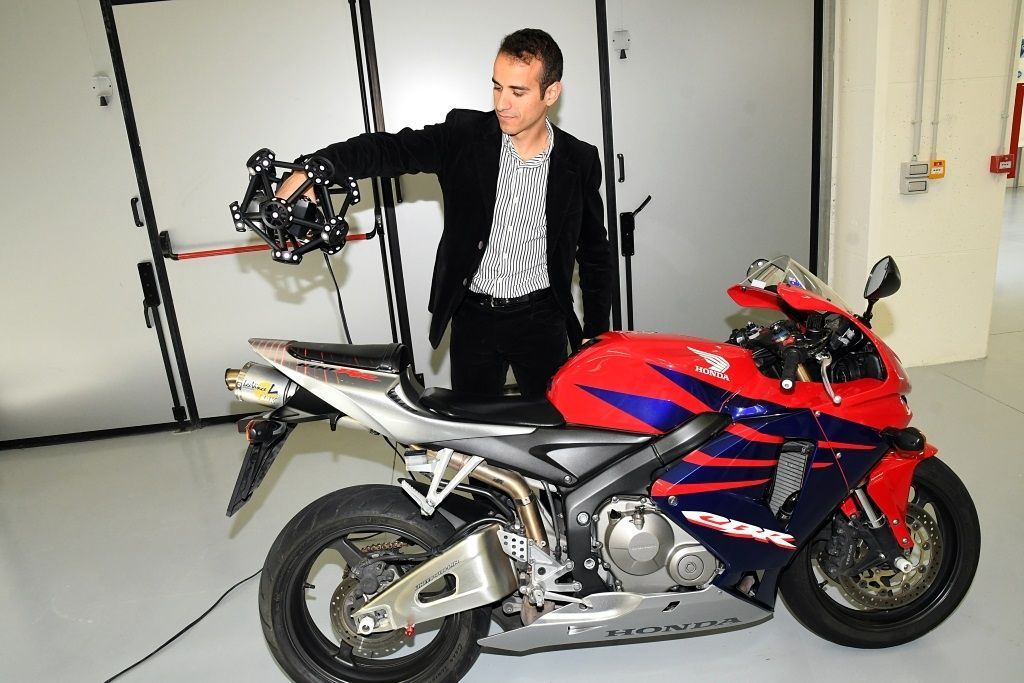
Le macchine al servizio delle aziende: Renishaw AM400
Ma cosa possono trovare le aziende nella facility? Per esempio, tra le stampanti, una macchina Renishaw AM400. La macchina funziona con diverse leghe di metallo a base di titanio, nichel, alluminio, cromo-cobalto, inox, cromo-cobalto per applicazioni dentali e titanio per applicazioni medicali. Secondo la società produttrice, «le polveri sono il risultato di ricerche approfondite e sono state testate per garantire un’elevata qualità alla luce di parametri di sistema affidabili e coerenti». Sempre secondo l’azienda «AM400 dispone di un sistema di somministrazione delle polveri dotato di valvole di esclusione, per consentire di ricaricare la polvere mentre il processo è in corso. Il sollevatore universale per il silo della polvere permette di rimuoverlo per pulirlo, o per sostituirlo con un altro nel caso di cambio di materiale. Questo semplifica grandemente il passaggio da un materiale ad un altro sulla piattaforma. I contenitori delle polveri restano all’esterno della camera e sono dotati di valvole di isolamento per setacciare in completa sicurezza la polvere non fusa, reintroducendola nel silo anche mentre il processo è in corso».
Comunque sia, funziona così: uno strato di polvere da 30 o 60 micron viene depositato su alcune piastre interne alla macchina. Dopo il passaggio del laser, emerge un pezzo di dimensioni e caratteristiche ben definite. Nella camera dove il processo si svolge, non c’è aria ma argon, perché alcuni metalli reagiscono in modo esplosivo con l’ossigeno. Secondo l’azienda produttrice, l’atmosfera inerte ultrapura e consumo di gas ridotto sono fra i punti forti della macchina. Essenziale, poi, per creare percorsi laser accurati, è il software di controllo, il Renishaw Optical Control System (OCS). L’azienda sostiene di averlo sviluppato internamente: «offriamo un sistema completamente integrato per controllare la direzione del laser e ottimizzare precisione, definizione degli elementi e finitura superficiale».
Altra caratteristica della macchina è la possibilità di utilizzare «parametri materiale aperti». La Renishaw definisce così il concetto: «Diversi metalli hanno diverse proprietà di fusione, quindi il software Renishaw offre all’utente un ulteriore vantaggio: la libertà di ottimizzare le impostazioni della macchina in base al materiale e alla geometria in lavorazione». Secondo Bosetti, grazie a questa macchina si possono realizzare «pezzi ad alto valore aggiunto, nella prototipia e nel dentale, per esempio».
Addizione e sottrazione: LASERTEC 65 3D.
Altra macchina la LASERTEC 65 3D. «Costa 1,2 milioni di euro, e ha la caratteristica di togliere e deporre materiale. Con questo dispositivo si possono riparare gli stampi e realizzare pezzi assai complicati, anche con superleghe difficili da trattare. In effetti, può trovare applicazione anche nel settore aeronautico, e cioè nella realizzazione di ugelli e camere di combustione» – ha affermato Gregori. Ma come si associano la fase additiva (con il laser) e quella “sottrattiva” (con la fresa)? Si parla di sinterizzazione laser con fresatura intergrata. Secondo l’azienda (DMG MORI) «si integra il processo di produzione laser generativo in una macchina di fresatura a 5 assi d’avanguardia. Questa soluzione ibrida combina la flessibilità della produzione generativa con la precisione della lavorazione ad asportazione truciolo, consentendo di realizzare pezzi completi con procedimento additivo nella stessa qualità dei finiti».
Sempre secondo l’azienda «questa tecnologia utilizza il processo di riporto di materiale applicato mediante un iniettore di polveri metalliche, che vanta velocità fino a 10 volte superiori alla produzione mediante letto di polvere». Il fatto di poter realizzare pezzi più grossi viene così spiegato: «Finora, l’applicazione di processi additivi si era limitata alla produzione di prototipi e pezzi piccoli, mentre oggi l’intelligente connubio della produzione additiva con iniettore di polveri e della lavorazione con asportazione di truciolo su un’unica macchina apre all’operatore orizzonti completamente nuovi in quanto a applicazioni e geometrie realizzabili. E sono soprattutto i pezzi di grandi dimensioni, che fino ad ora necessitavano di lunghe lavorazioni meccaniche, a godere del vantaggio di una produzione innovativa e redditizia». Secondo Collini «il risultato dipende anche dalla qualità delle polveri: più i grani sono uniformi, rotondi e fini, meglio è. La macchina consuma circa 50 Kw».
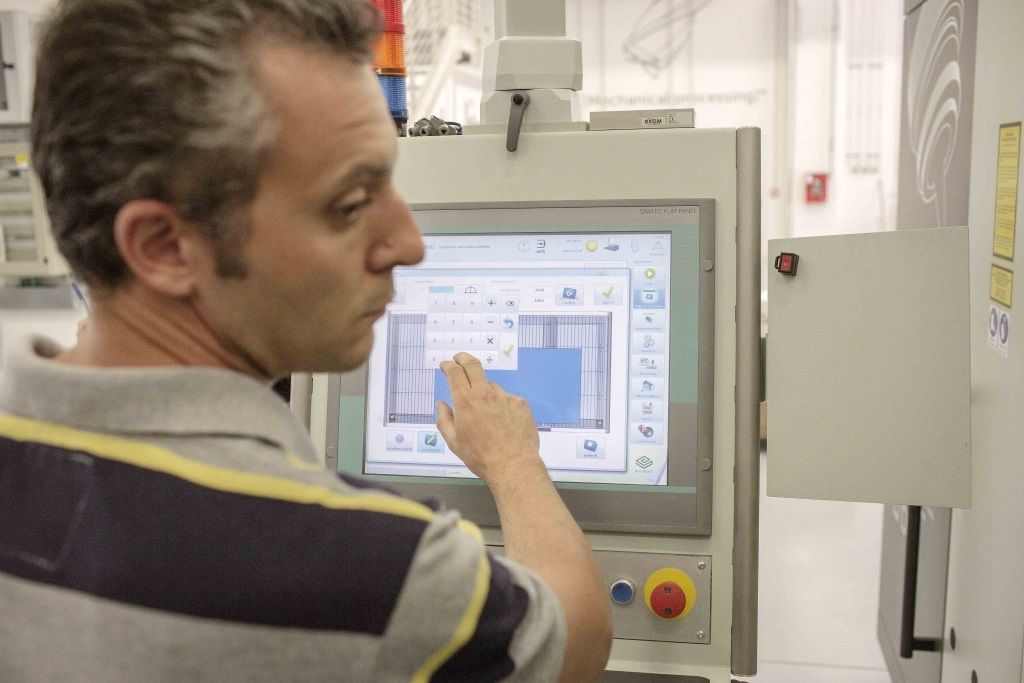
Laser per il taglio di tubi e lamiere:LC5 del BLM GROUP
Fra le tante macchine, quella più grande ha le dimensioni di un miniappartamento. Stiamo parlando della LC5 del BLM GROUP. Si tratta di una macchina laser in grado di tagliare sia tubi che lamiere. Può trattare acciaio, inox, ottone, rame, alluminio. Secondo l’azienda produttrice, «il passaggio dalla lavorazione della lamiera al tubo è immediato, sia in un senso che nell’altro, senza dover riconfigurare o riattrezzare la macchina. Così è possibile sfruttare ogni minuto per far produrre l’impianto e ottimizzi l’investimento». Il carico e lo scarico dei tubi avviene automaticamente. «Il caricatore – rende noto l’azienda – estrae le barre dal fascio, una dopo l’altra, e le porta sulla linea di lavoro in modo continuo senza interventi manuali. Pertanto è possibile trovare i pezzi tagliati già scaricati e accumulati in cassa. Gli sfridi (scarti, ndr) invece finiscono in un contenitore a parte, così la macchina è sempre pulita e al massimo della sua efficienza». Il formato lamiera può avere diverse configurazioni: 3 metri per 1,5; 4 per 2; 6 per 2. Il cambio del pallet lamiera è elettrico. Sempre secondo l’azienda, «due pannelli sul lato lamiera e sul lato tubo, entrambi liberamente orientabili, consentono di avere il controllo sul processo».
La sorgente laser è in fibra sino a 6 Kw. Ciò consentirebbe «di abbattere drasticamente i consumi elettrici dell’impianto, determinando non solo risparmi sulla bolletta elettrica ma anche maggior facilità di installazione poiché non è necessario sovradimensionare la fornitura elettrica». Inoltre, sempre per il produttore, «la maggior velocità del laser in fibra nel taglio in azoto di spessori sottili determina una produttività della macchina più che doppia rispetto al laser CO2: acciaio da costruzione e acciaio inossidabile di medio basso spessore sono i materiali che maggiormente si avvantaggiano della fibra». Infine l’azienda sottolinea che «rame e ottone, materiali fino ad oggi proibiti con la tecnologia CO2, sono ora facilmente tagliabili con il laser in fibra. Anche alluminio e acciaio zincato, da sempre problematici, non hanno più limitazioni». Assistere al taglio di tubi e lamiere è, in un certo qual modo, un’esperienza. Si vede il laser scavare nel duro acciaio con tanti piccoli lampi di fuoco. Collini ha poi ricordato che la macchina è in comodato gratuito.