La digital transformation è un beneficio di filiera. Lo scambio di flussi informativi tra l’azienda e i suoi clienti e supplier, se muniti della strumentazione per interpretarli, porta alla sincronizzazione del meccanismo della fornitura, e quindi ad una maggiore efficienza operativa di sistema. Eppure, molte imprese continuano ad organizzarsi in silos informativi; i dati restano confinati nei dipartimenti, inaccessibili ad altri comparti e divisioni e ai loro contractors. Ciò produce effetti negativi sulle performance di tutti gli ambiti coinvolti, interni ed esterni all’azienda.
Lo pensa il global head of solution management di Sap Mike Lackey, che nel suo intervento al World Manufacturing Forum di Cernobbio, “Digital supply chain for Manufacturing” ha introdotto un nuovo modello organizzativo: la digital supply chain, che comporta piena visibilità e comunicazione tra dipartimenti, grazie ad uno scambio circolare dei dati. Deve essere, per Lackey, connessa, predittiva e intelligente, e cioè dotata di strumenti avanzati di intelligenza artificiale per preconizzare trend e abilitare modelli di business innovativi.
Dispositivi di cui Sap, la multinazionale tedesca del software gestionale, già dispone. Ad esempio Sap Leonardo, piattaforma integrata, aperta e flessibile, che collega i dati di fabbrica a quelli del business, e al contempo infonde intelligenza alle applicazioni dei gestionali. Ma anche Sap MII (Sap Manufacturing Integration and Intelligence), che integra l’Erp con i sistemi di campo, e Sap Digital Manufacturing Insights, che fornisce analisi utili alla definizione di scelte strategiche, elaborando i dati raccolti con l’IoT in Sap Cloud Platform, dove lavorano sofisticati software di analytics dotati di algoritmi avanzati.

Le quattro “ère” della trasformazione digitale
La trasformazione digitale è un viaggio in quattro step fondamentali, alcuni dei quali non sono ancora stati compiuti dalla maggior parte delle aziende. Se ne è discusso in via teorica, per tracciare un viatico. Più che di step, per Mike Lackey è opportuno parlare di «quattro ère» distinte, nel senso che descriverebbero un progresso dalla a alla z dello stato dell’arte, che poi troverebbe riscontri quantificabili in termini di produttività. La prima èra è quella dell’automazione industriale, e quindi quella della gestione delle macchine da lavoro grazie a sistemi di controllo come ad esempio i Plc (controllori logico-programmabili), che eseguono piani definiti ed elaborano segnali provenienti da sensori. Protagonisti, anche, gli attuatori, i sensori, i trasduttori, i sistemi di visione artificiale e i micro controller. È un percorso, quello dell’automazione industriale, che non ha fine, ma che anzi continua con strumenti sempre più sofisticati. E cha ha comportato – e continua a farlo – la sostituzione di una parte del personale.
La seconda è la business process automation. Si tratta dell’automazione dei processi industriali, distinta dall’era precedente perché intesa in senso lato: comporta la raccolta dati e la loro elaborazione per l’efficientamento dello shopfloor intero e non solo: incide in aree diverse, come il marketing, le vendite e i flussi di lavoro. La tendenza è quella di utilizzare sempre di più l’intelligenza artificiale, perché questa è in grado di interpretare set di dati non strutturati e di interagire con gli esseri umani interpretando il loro linguaggio naturale.

La terza è la trasformazione digitale, èra isolata dalle altre perché afferente ad un contesto ancora più lato: grazie all’analisi dei dati, vengono estratte informazioni che consentono di erogare nuovi servizi e far vivere esperienze mai sperimentate prima dal consumatore, creando pervasivamente nuove connessioni tra persone, luoghi e cose. Si pensi alla servitizzazione del prodotto.
Infine, secondo Lackey, l’èra dell’intelligent enterprise. Per la verità, quest’ultima più che un periodo definito da una tecnologia particolare, è un approccio di gestione, che mette insieme da una parte l’intelligenza che scaturisce dai più sofisticati software di analytics e dalle tecnologie predittive, dall’altra la visione strategica, frutto della sintesi tipicamente umana di competenze trasversali e specialistiche. Grazie a questa strategia, i dati raccolti dai sensori possono essere trasformati in azioni in tutte le linee di business, sbloccando nuove aree di crescita. L’intelligent enterprise è l’approccio che Sap ha adottato, per intenderci.

I trend globali della manifattura e la digital supply chain
In questo contesto che vede l’industria attraversare ere di sviluppo tecnologico crescente, Lackey scorge tre trend che interessano in particolare la manifattura a livello globale. Anzitutto, la customer centricity, e cioè il crescente rilievo attribuito ai bisogni individuali dei clienti finali, che incidono sempre di più sulla realizzazione del bene-servizio loro destinato. Di qui il passaggio dalla produzione di massa alla personalizzazione di massa – con tutto ciò che comporta in termini di efficienza dei processi e di costo.
Poi la visibilità totale: da aziende basate sulla circolazione di documenti cartacei e sul dominio dei silos informativi, a quelle dove lo scambio di informazioni avviene per via orizzontale e verticale e tramite dispositivi digitali o mobili.
Infine, la business innovation, che indica il progresso dai processi manuali a quelli altamente automatizzati, dalle linee di produzione “materiali” ai sistemi cyber-fisici, dalla manifattura di prodotto alla servitizzazione.
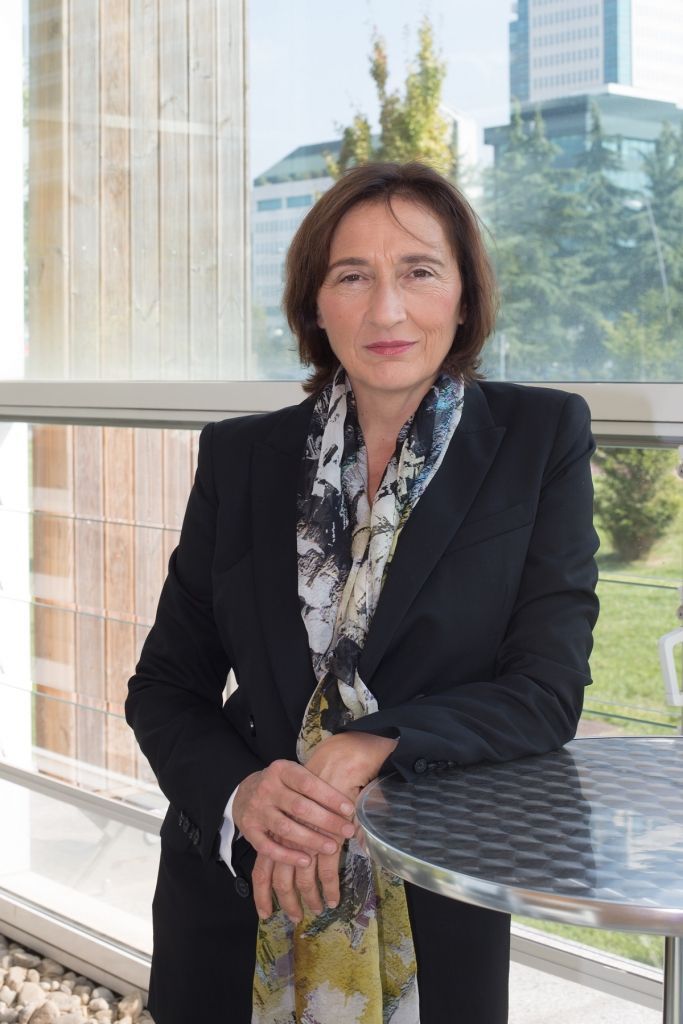
Solo che, per Lackey, la mancata diffusione di dati da un comparto aziendale all’altro, i sistemi disconnessi e i processi manuali producono effetti negativi sulle performance aziendali. Da una prospettiva “verticale” il trasferimento di informazioni dovrebbe avvenire biunivocamente dalle macchine alle linee, dalle linee all’impianto, e da questo agli altri stabilimenti, alla sede dell’azienda e anche ai produttori a contratto. Secondo una prospettiva “orizzontale”, le aziende da una parte vorrebbero interconnettere l’intera catena dei fornitori, dall’altra continuano a organizzarsi in silos dipartimentali: design, manufacture, deliver e operate restano distinti.
Anzitutto, per Lackey, si deve organizzare una digital supply chain, che comporti piena visibilità e comunicazione tra dipartimenti, grazie ad uno scambio circolare dei dati. La pianificazione, l’analisi e l’esecuzione sono così orchestrate di volta in volta, affrontando le fasi operative critiche sulla scorta di input e requisiti valutati real time. In questo modo, la struttura si fa reattiva, veloce e resiliente. Ma che c’entra la supply chain? C’entra, perché i dipartimenti si riferiscono a contractors diversi. Per esempio: la produzione ha un certo fornitore, e la progettazione collabora con uno studio esterno o si serve di un software di questa o quella multinazionale. Per Lackey solo la circolarità del processo informativo interno mette assieme sia i flussi interni che quelli esterni, relativi ai contractor.

Vantaggi della digital supply chain dal design all’operate
Secondo Lackey, il modello distributivo circolare delle informazioni tra i dipartimenti produce vantaggi per ognuno di essi. Per esempio, per il design comporta la possibilità di innovare continuamente, progettando in base alla domanda del cliente; per l’organizzazione, quella di ottenere una visione olistica della domanda; per l’impianto produttivo, quella di ottimizzare i processi manifatturieri migliorando la collaborazione con i fornitori e incrementando l’agilità del sistema; per il settore vendite e consegne, quella di accrescere l’utilizzabilità di magazzini e trasporti, e di aumentare la velocità, l’efficienza e la sostenibilità del processo; per le operation, quella di gestire in modo efficiente il ciclo di vita degli asset fisici e quella di predire e simulare il loro comportamento evitando inattesi downtime.

La struttura della digital supply chain
Anzitutto, la digital supply chain dev’essere “connected”. Macchine, partner e processi, dal design alle operation, devono comunicare tra di loro. In secondo luogo, deve essere “predictive” cioè deve preconizzare i risultati dei processi e i comportamenti degli asset, per abilitare modelli di business innovativi. Infine, deve essere “intelligent”, perché un utilizzo intelligente (e cioè basato su modelli avanzati di AI) dei dati valutati real time, può fornire un’esperienza unica al cliente. Quanto alle tecnologie utili, va ricordato che la multinazionale tedesca dispone di Sap Leonardo, piattaforma integrata, aperta e flessibile, che collega i dati di fabbrica a quelli del business, e al contempo infonde intelligenza alle applicazioni dei gestionali.

Si può fare l’esempio si Sap CoPilot, l’Alexa del software gestionale: grazie all’Ai, per utilizzare le app che orchestrano i processi aziendali non è più necessario conoscere uno specifico linguaggio informatico; basta rivolgere una domanda al sistema. Sap CoPilot è in grado di comprendere l’intento del richiedente. E poi c’è Irpa. È un software che semplifica il lavoro degli impiegati, perché si occupa di risolvere senza l’intervento umano molti step burocratici e formali che normalmente avrebbero richiesto una attività manuale. In questo articolo di Industria Italiana si può reperire un esempio: un utente, che lavora in azienda, vuole acquistare un Pc. Normalmente entra nel sistema acquisti; fa una ricerca tra l’hardware, sceglie il modello, il laptop, il colore e altri particolari; dopodiché fa una richiesta di acquisto che viene inoltrata al manager del centro di costo, e se questi dice sì, l’ordine viene trasmesso al fornitore che fa partire l’approvvigionamento e la spedizione. È possibile semplificare tutto. Per esempio, si può si può scattare una foto digitale dell’identificativo del prodotto che voglio ordinare, inserirla in sistema e procedere all’acquisto». In pratica, grazie al machine learning, il sistema realizza tutti gli step che l’utente avrebbe dovuto compiere manualmente.

Le soluzioni Sap MII e Sap Digital Manufacturing Insights
Tenuto conto di tutte questa esigenze, a livello di macchine, la multinazionale dispone della soluzione Sap Connectivity e altre come Sap MII (Sap Manufacturing Integration and Intelligence: integra l’Erp con i sistemi di campo) e Sap Manufacturing Execution Systems, il Mes della multinazionale. Ma per tutti gli altri livelli, dall’impianto regionale all’impresa globale, lo strumento giusto, secondo l’azienda, è Sap Digital Manufacturing Insights. La questione è quella delle decisioni tattiche e strategiche da prendere per ottenere le migliori prestazioni di processo. La soluzione promette di fornire analisi olistiche utili allo scopo, mettendo insieme i dati raccolti con l’IoT e la loro elaborazione in Sap Cloud Platform, dove lavorano sofisticati software di analytics dotati di algoritmi avanzati e di machine learning. Questi, secondo la multinazionale, consentono all’azienda-utente di tracciare e analizzare tutta la produzione degli stabilimenti in giro per il mondo, e di fare previsioni di valore strategico; di acquisire dati da diversi sistemi operativi e di automazione, e di renderli visibili su interfacce standard; e di accelerare l’analisi dei problemi per supportare il miglioramento continuo.

Casi di applicazione della digitalizzazione della supply chain: il controllo antifrode in acciaieria con MII.
Si immagini un’industria del settore dell’acciaieria. Ogni giorno, camion ripieni di materiale grezzo si presentano alla pesa: il metallo in entrata viene pagato in base a questa operazione. Può capitare che si verifichino frodi: tra cumuli di metallo fondibile, può possono reperirsi sostanze inutili o dannose per il processo. Una vecchia lavatrice può contenere componenti non metalliche che non sono state separate ed accantonate prima della misurazione. Di questo problema si è occupata Minsait, brand di Indra, società di consulenza e system integrator quotata alla Borsa di Madrid. Più di 3,1 miliardi di fatturato, 43mila dipendenti, presenza in 46 Paesi e operazioni commerciali concluse in più di 140 Paesi: questo l’identikit di Indra. Secondo Santi Maisano, responsabile area Sap per il mercato industriale di Minsait Italia «inizialmente eravamo stati chiamati ad implementare l’automazione del magazzino di una importante acciaieria italiana; poi ci è stato anche affidato il compito di gestire le attività di logistica inboud, e cioè di approvvigionamento e stoccaggio del materiale, e in chiave 4.0». E quindi il controllo degli automezzi in entrata nel plant, la stazione bilancia e il quality check point. Per evitare il reiterarsi delle frodi, si è digitalizzato lo storico relativo a camion e patenti coinvolte. Questi dati vengono confrontati da Sap MII con quelli emergenti da lettura codici e da telecamere. Nei casi di positività, il sistema allerta gli operatori di campo che ricevono informazioni in una chatbot su mobile o tablet. In futuro, i controlli saranno effettuati da droni, ha reso noto Maisano.

Casi di applicazione della digitalizzazione della supply chain: come ottimizzare i taglio della materia prima nella produzione di suole con Robochain
La Vibram di Albizzate (Varese), azienda fondata nel da Vitale Bramani nel 1937, produce suole di gomma per calzature, in particolare scarpe destinate all’impiego in montagna nelle scalate. Con un fatturato di 125 milioni e più di 800 dipendenti, è presente in 20 Paesi. È l’impresa che ha inventato la suola a “carro armato”. Gradualmente, il modello di business si è evoluto: prima era solo B2B, ora è anche B2C. L’azienda, secondo il global It manager Virginio Basilico, si è resa conto che processi interni ed esterni vanno regolati da un solo core intelligente in grado di elaborare dati. Occorre sviluppare e integrare servizi, associare l’engagement con l’ecosistema di clienti e fornitori a quello con i consumatori finali. Ma l’azienda aveva un problema in particolare. Ritagliare il materiale per produrre una suola significa necessariamente scartarne una parte. Limitare gli scarti avrebbe portato ad un incremento dell’efficienza e della marginalità.

Si è rivolta pertanto ad Altea Up, società del gruppo Altea Federation. La seconda è una federazione di aziende dedicate alla consulenza direzionale e informatica per progetti di trasformazione digitale. Ha sede a Lainate (Milano). Con 1.200 dipendenti, fattura 102 milioni. Le società del gruppo sono Altea, Nextea, Altea People, Alterna, AlteaIn, Altea365, Altea Digital, Plm Systems e AlteaUp. Quest’ultima, 35 milioni di fatturato e 300 dipendenti, è quella specializzata in soluzioni Sap. Comunque sia, per risolvere il problema, Altea Up si è rivolta ad un docente universitario, «Giuseppe Greco – ha affermato il Ceo di Altea Up Roberto Gemma – che ha trovato il modello matematico per ottimizzare il disegno delle sagome e evitare sprechi. Dopo un insieme di test, con la formula si è fatto Robochain, un risolutore matematico che gira su Sap Cloud Platform». Robochain è una soluzione out of the box, che grazie alla potenza di calcolo installata su cloud risolve in 10 minuti problemi che prima venivano superati in più giorni: tra i vantaggi, una significativa riduzione dei tempi di set-up e di costi. È legata a Sap Leonardo, piattaforma di cui abbiamo già parlato.
