di Filippo Astone ♦ Stefano Brandinali, Cio della multinazionale dei cavi, racconta la digital transformation in corso e i suoi principali obiettivi. Potrebbe essere un esempio di come il 4.0 funziona davvero e produce quindi valore economico reale
Il primo passo è stato fatto a Calais, ma non si tratta dell’invasione della Normandia per salvare il mondo dai nazisti. Qui il protagonista è Prysmian, che ha scelto il proprio stabilimento francese come pioniere di una trasformazione digitale radicale, con obiettivi importanti in termini di aumento dei ricavi e della produttività. Il progetto, chiamato “Fast Track”, rappresenta un passo in avanti nell’attuazione del programma “Fast Forward Operations” della società guidata da Valerio Battista. Lo scopo è di creare stabilimenti più smart facendo leva sull’integrazione tra competenze digitali e know-how delle persone.

E’ realizzato in collaborazione con Dassault Systèmes e 3DEXPERIENCE Company. Prysmian l’ha annunciato nei primi giorni di novembre. Adesso Industria Italiana, grazie a una approfondita intervista con il Cio Stefano Brandinali, è in grado di fornire maggiori particolari. Ricordiamo che Prysmian ha ricavi per 7,6 miliardi di euro, 21mila dipendenti, 82 stabilimenti in 50 Paesi. Nasce dalla trasformazione della parte cavi di Pirelli, che Marco Tronchetti Provera cedette nel 2005, all’epoca di Telecom. Dopo 12 anni, grazie anche ad alcune acquisizioni (la più importante delle quali è rappresentata da Draka) è diventata assai più grande e ha una fisionomia molto diversa. E’ l’unica public company quotata alla Borsa di Milano.

Ogni attività viene tracciata: così si conquista un importante vantaggio competitivo
«Calais è il primo passo. Tracceremo ogni nostra attività. L’idea è di avere un’unica piattaforma, da esportare in tutti gli stabilimenti, che parleranno così la stessa lingua. A partire dal primo trimestre 2018, stiamo pensando di intervenire su almeno 15 fabbriche all’anno del settore cavi, che in tutto sono circa 70. Il nostro piano di roll out, pertanto, è assai aggressivo», spiega Brandinali. Ma la tracciabilità, fino ad oggi, non sembrava un tema molto sentito nel mondo dei cavi. «E’ vero. Adesso invece i clienti iniziano a chiedercela». Perché? «Per spiegarmi meglio farò un esempio tratto dal mondo dell’aerospaziale. In quel settore ci sono tematiche di sicurezza per cui ci deve essere la tracciabilità fino al lotto della materia prima. Ora sarà possibile anche per i cavi. Con la nuova organizzazione 4.0 delle nostre fabbriche, l’operatore registra ogni singola fase, la macchina dice quando è iniziato, quando è finito e a ogni step noi mettiamo un bollino con il lotto dello step, il lotto della fase. A quel punto se c’è un problema sul prodotto finito, siamo in grado di risalire interamente la catena, cosa che prima non era possibile».
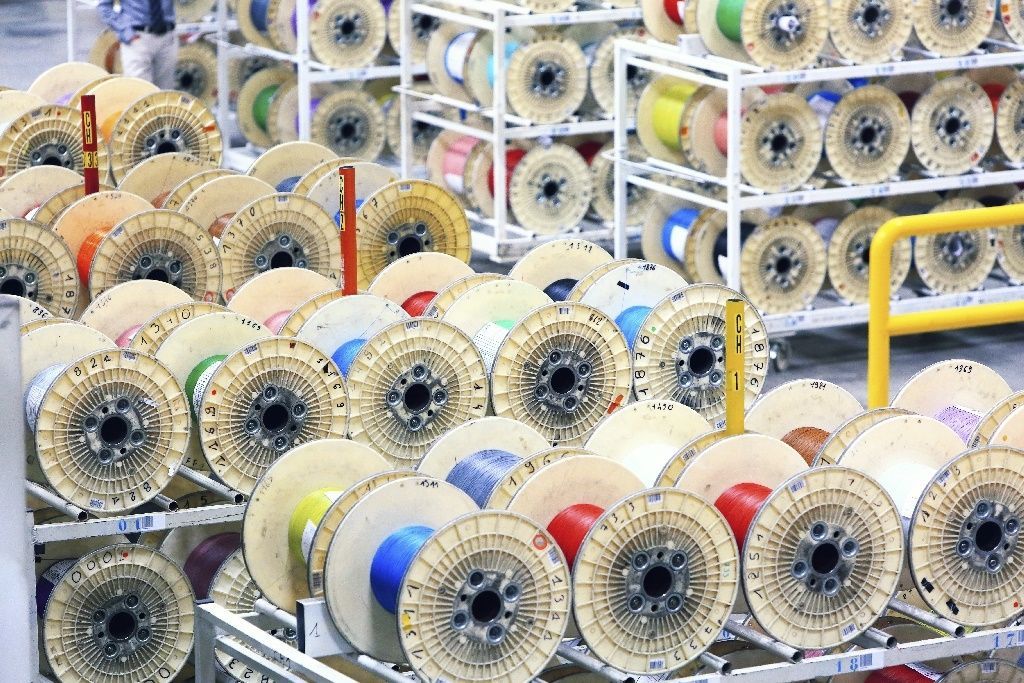
Oltre alla tracciabilità, è facile supporre che l’obiettivo sia il miglioramento della produttività. «Certo. Ma non si tratta solo di un tema quantitativo: l’obiettivo di tutto il progetto “Fast Forward Operations” è migliorare il servizio al cliente. Quindi in questo senso la tracciabilità non è un fattore di efficienza per noi ma è un fattore di garanzia al cliente. Noi che siamo il market leader ora vogliamo dire al nostro cliente “Sappi che noi possiamo tracciare fino alla materia prima.” I nostri competitor ad oggi non possono. il vantaggio è evidente. Quindi è un investimento industriale che genera valore commerciale».

Best practise messe a fattor comune: “fatto e sviluppato con loro”
In Prysmian il processo di digital transformation rappresenta anche un’occasione per mettere a fattore comune sia le best practise sia le soluzioni a problemi avvertiti come importanti. «Noi non abbiamo scelto un sistema e non abbiamo rivisto un processo calandoli dall’alto. Abbiamo preferito un approccio diverso. Abbiamo chiamato i colleghi, abbiamo messo l’operatore al centro, e abbiamo chiesto loro: “Che cosa non funziona e che cosa funziona ? Cosa vi piace, cosa non vi piace dei processi di oggi?”. E abbiamo lavorato sulle risposte ottenute. È chiaro che il fine principale è la manutenzione predittiva, l’Iot e tutta una serie di attività che stanno sotto il cappello 4.0. Ma è anche importante ottimizzare ciò che è ottimizzabile. Infatti, lo slogan che abbiamo utilizzato è “fatto e sviluppato con loro, per loro”. Dove “loro” sono i nostri dipendenti».

Il principio è di creare nuovi processi senza stravolgere quelli precedenti
«La nostra idea è stata quella di creare un layer digitale sopra il mondo fisico senza stravolgere il nostro modo di fare i cavi e le nostre linee di produzione. Non abbiamo cambiato le linee ma abbiamo messo dei sensori IOT, le linee sono quelle di prima , in alcuni casi sono linee anche solide, mature, stiamo parlando di linee che possono avere anche 30 anni di vita, ovviamente mantenute, aggravate in alcuni componenti». Il punto, insomma, è l’intelligenza che viene messa sopra le linee. La creazione di valore arriva da lì.
Manutenzione predittiva ma soprattutto intelligente
La manutenzione predittiva è uno degli imperativi categorici della teoria 4.0. «Noi misuriamo i parametri più importanti delle macchine, come la velocità o la temperatura degli estrusori. Report e dashboard che sono direttamente sul terminale di un operatore e permettono all’operatore di intervenire, per esempio, rallentando la macchina prima della rottura. Il tutto viene fatto con intelligenza, e la decisione finale dipende dall’uomo, che riceve però le informazioni migliori. Così, ad esempio, si può decidere che è meglio finire un ciclo di produzione e poi chiamare gli addetti alla manutenzione».
Barcode come strumento diffuso di tracciabilità
«Ora si è deciso di etichettare tutte le location così l’intero processo è guidato ed è il device stesso, quindi il sistema, che indica le cose da fare e quelle che invece non sono possibili. In precedenza, a Calais i codici a barre non erano utilizzati se non nel magazzino delle materie prime. Oggi sono ovunque: sul lungo macchina, ma anche nelle location dove ci sono le bobine vuote. Quando l’operatore deve caricare una bobina – perché sulla bobina andrà il cavo prodotto – il sistema gli ricorderà dapprima quale cavo è in produzione, a quale ordine di produzione risponde e che deve andare a recuperare la bobina in una determinata location. Una volta raggiunta la location dove si trova la bobina il barcode che la identifica viene interrogato dal device dell’operatore il quale saprà se è quella giusta oppure no. Tutto questo processo prima non c’era. Sebbene fossimo in un’organizzazione molto evoluta (magazzino delle bobine ben ordinato, le linee di produzione con ottime velocità, qualità delle macchine buona) non esisteva questo tipo di automazione della raccolta continua delle informazioni. Automazione che, fatto non trascurabile, tende a evitare l’errore umano, che ovviamente è sempre possibile».

Big Data in fabbrica
«Sostanzialmente il nostro principio ispiratore è di disaccoppiare i dati che raccogliamo dalle macchine in modo automatico dall’operatività dell’utente. Disaccoppiando il flusso industriale automatizzato della macchina dal flusso operativo dell’operatore, rendiamo le due azioni parallele. In estrema sintesi: prima di Fast Track era l’operatore a dire cosa stava succedendo sulla macchina. Ora avviene l’opposto. Per fare un esempio, l’operatore in passato diceva: “Sta iniziando la fase alfa, nella quale la macchina sta facendo queste cose, con questa velocità, con questa temperatura, con questi dati presi dal campo”. Al termine l’operatore affermava : ” …è finita questa fase, spengo la macchina, stacco la bobina, la porto nella seconda fase di produzione (dove ad esempio avviene l’avvolgimento di più fibre in un unico cavo)”.
Oggi gli impianti parlano direttamente col sistema per tutto ciò che riguarda i dati di macchina, quindi sono più puntuali, più precisi. Stiamo parlando di Big Data, raccogliamo molti più dati di prima, che permettono anche di misurare cosa fa l’operatore. Insomma c’è una misurazione, ovviamente in termini costruttivi, sia di come sta andando la macchina per anticipare eventuali cali di velocità o aumenti di temperatura anomali ma anche dell’operatore. L’operatore a quel punto può dedicarsi ad altre cose mentre sta guardando la macchina: può, per esempio iniziare a preparare la linea successiva. Ecco dunque come otteniamo l’obiettivo del disaccoppiamento. Quindi la misurazione, per esempio il costo del prodotto, diventa una misurazione puntuale ed actual, non elaborata su basi mediate storiche».

Miglior controllo delle macchine
In passato l’operatore scriveva molto, digitava molto. Oggi l’operatore dispone di handheld ( device senza tastiere del tutto simili a un tablet o uno smartphone ) e non digita più ma in ogni singola fase dispone di “QR code” ovvero di barcode su cui l’operatore clicca. il “QR code” dà l’ indicazione corretta. Risultato: maggior guida e controllo per l’operatore; minor possibilità di errore perché si imputa (ovvero non è l’uomo a immettere dati) il meno possibile. Un fatto importante è che adesso c’è un miglior controllo delle macchine: sono le macchine stesse che in tempo reale comunicano lo stato di funzionamento. In precedenza, invece, era un processo asincrono, posticipato.

Gemelli digitali
Per noi l’Industry 4.0 comprende anche i cosiddetti Digital Twin. In altre parole, si tratta di potenti software che consentono la duplicazione digitale del mondo fisico, potendo poi intervenire indirettamente sul mondo fisico stesso. Ad esempio, come si diceva prima, nelle nostre fabbriche vengono raccolti molti dati di velocità e di temperature. Grazie a quei dati, io operatore riconosco che alcuni fenomeni stanno avvenendo nel mio gemello digitale e agisco poi sul fisico, disponendo di precise indicazioni sul da farsi. Passo successivo? Farlo in automatico: fare in modo che la macchina si auto setti rispetto alle basi storiche».