di Gaia Fiertler ♦ Dallo svecchiamento del marchio alla lean production, fino alla digital transformation. Ecco il percorso che ha portato una delle più importanti aziende italiane del food and beverages (Amaro Montenegro e Vecchia Romagna, Olio Cuore, Bonomelli, Polenta Valsugana e Cannamela) con la supervisione di Kpmg, verso lo smart manufacturing. Con vantaggi per il business e l’organizzazione aziendale
Una nuova strategia commerciale che ha richiesto innovazione di prodotto. L’impatto sulla produzione che ha avuto bisogno di introdurre la lean production per garantire efficienza ed efficacia. Una reportistica manuale lenta e dispendiosa, che ha avuto bisogno di digitalizzare i processi per avere evidenze oggettive in tempo reale. Questo il percorso in quattro tappe avviato dal Gruppo Montenegro (noto per i suoi brand iconici tra cui Amaro Montenegro e Vecchia Romagna, Olio Cuore, Bonomelli, Polenta Valsugana e Cannamela) nel 2014 in seguito alla nomina del nuovo amministratore delegato, Marco Ferrari. L’azienda tra i diversi driver di crescita, ha puntato sullo sviluppo del canale Super Ho.Re.Ca., che comprende i locali di tendenza, i “mixology bar” e il mondo della notte.

Prima tappa: innovazione di prodotto
La strategia commerciale parte dal prodotto e dallo “svecchiamento” del marchio: viene disegnata una nuova bottiglia per l’amaro Montenegro (prodotto dal 1885), si studiano nuove combinazioni per i cocktail e si riposiziona il brand attraverso una nuova campagna di comunicazione. Sul fronte distributivo viene rafforzata la rete di agenti, viene completata l’offerta al Super Ho.Re.Ca. con contratti di distribuzione di spirit internazionali sul mercato italiano e vengono sviluppati i mercati internazionali, con particolare focus negli Stati Uniti. Il Gruppo, che comprende la divisione food Bonomelli srl e la divisione spirit Montenegro srl, con 230 milioni di euro di fatturato nel 2017, conta 330 dipendenti distribuiti nei tre stabilimenti (San Lazzaro e di Zola Predosa in provincia di Bologna e in Dolzago in provincia di Lecco) e nell’headquarter di Zola Predosa.

Seconda tappa: lean production
L’innovazione di prodotto e di packaging per supportare la nuova strategia commerciale impatta sulle linee produttive che si fanno più flessibili, garantendo efficienza e qualità. «Noi delle Operations siamo stati subito coinvolti in un cambiamento che è prima di tutto culturale, perché si passa all’improvviso da una logica di “mantenimento” a una logica di miglioramento continuo. E nella metodologia lean viene individuata la via da seguire con un approccio bottom up», racconta Paolo Silipo, direttore Operations Gruppo Montenegro. I direttori dei tre impianti, il responsabile dell’ingegneria, quello della sicurezza e i due della qualità vengono invitati a fare un tour esplorativo presso quelle, tra le grandi aziende del food, che hanno già applicato la lean production. Partendo da queste rilevazioni, viene ingegnerizzato un progetto di lean da applicare alla produzione del Gruppo.

Terza tappa: reportistica manuale del funzionamento delle macchine
Per oltre due anni, dal 2015 al 2017, il monitoraggio delle performance viene fatto con una rilevazione manuale dell’andamento della produzione, dei rallentamenti e dei fermi macchina. Il processo, oltre a essere lento e poco attendibile, richiede un considerevole impiego di risorse perché, quotidianamente, a fine giornata tutti i dati raccolti sui moduli cartacei vengono trascritti su un software di analisi, i cui risultati vengono discussi la mattina dopo a inizio lavorazione dai vari capi-reparto e manutentori, con ampio spazio a interpretazioni personali. L’azienda si rende conto di essere arrivata a un limite nell’utilizzo della lean production.
Quarta tappa: digitalizzazione dei processi
A questo punto il Gruppo si rivolge a Kpmg Advisory per essere aiutata a superare questo limite di avanzamento nel presunto miglioramento continuo. «Per essere efficiente la metodologia lean aveva bisogno di tecnologie abilitanti. La lean ci insegna la forza di visualizzare quello che succede, ma senza il supporto tecnologico la manualità nella raccolta delle informazioni rallenta il processo di monitoraggio e di intervento per risolvere le problematiche, non risolvendo in modo definitivo le inefficienze», commenta Carmelo Mariano, partner Kpmg Advisory. L’azienda utilizzava già Sap Erp per il controllo di gestione, ma non per la produzione.
Nel software Sap Manufacturing Integration&Intelligence viene individuato lo strumento più adatto a una media azienda per la sua capacità di integrarsi con il campo, per la flessibilità nel disegnare i processi di fabbrica e per l’interfacciabilità altamente “user friendly” per gli operatori. Sei-sette capireparto e una ventina di capilinea vengono dotati di tablet industriali, su cui oggi appaiono in tempo reale le non conformità. Via via che gli operatori selezionano l’origine della non conformità (una macchina a monte o a valle), scelgono tra una rosa di possibili cause. «La visualizzazione sul tablet è nel linguaggio naturale, lasciando agli informatici in ufficio l’analisi dei codici sottostanti. Ora sappiamo che cosa succede, i sensori sono collegati al sistema informativo aziendale, cui vengono fornite molte più informazioni di prima. Su queste gli ingegneri possono lavorare per risolvere determinati problemi all’origine e, al tempo stesso, agli operatori viene offerta l’immediatezza sul funzionamento della linea con la possibilità di intervenire in fretta», aggiunge Matteo D’Ulisse, manager Kpmg Advisory.
«Al momento si chiede ancora all’operatore di aggiungere delle informazioni al sistema, selezionando tra elenchi di possibilità, anche perché non tutte le macchine sono ancora collegate fra loro e al sistema centrale, ma in prospettiva potrà essere completamente automatizzata l’individuazione delle cause di un fermo macchina, anche attraverso delle telecamere collegate.» Il progetto segna l’avvio dello smart manufacturing, ossia dell’introduzione dei concetti di Industry 4.0 anche in un’azienda storica come Montenegro, dimostrando che per crescere non si può prescindere dal nuovo linguaggio digitale. Su 47 macchine ad oggi sono integrate tra loro 21, selezionate tra quelle più nuove e collegabili senza costi e tempi eccessivi.
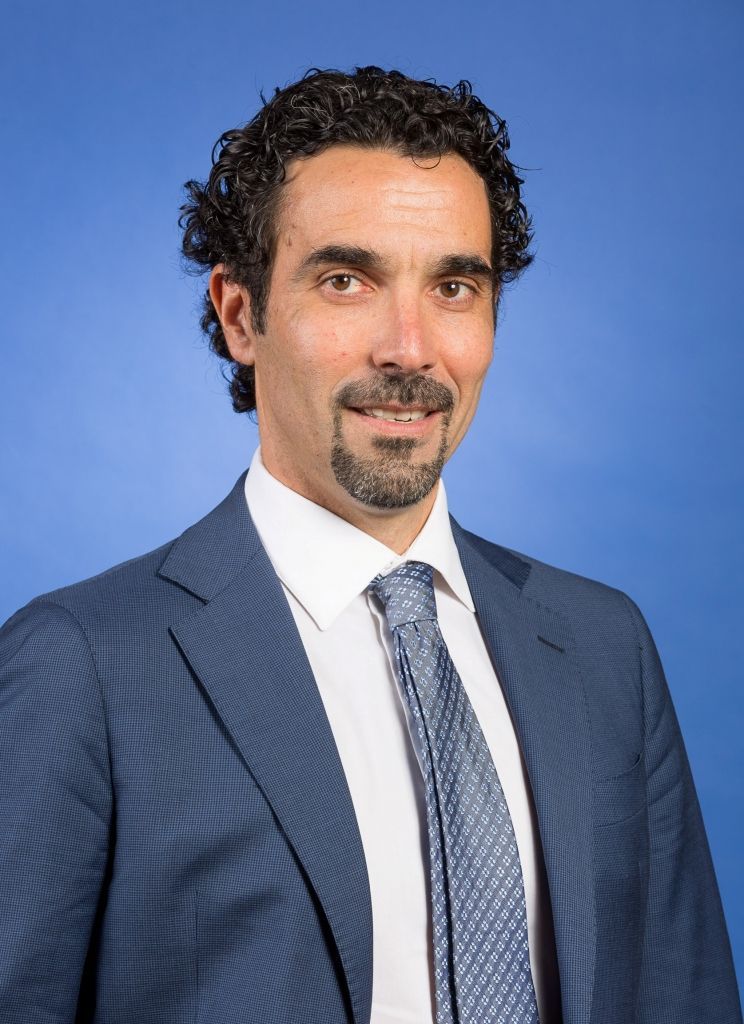
Gli obiettivi del progetto
A monte della realizzazione c’è stato un progetto di architettura seguito da Kpmg che, tra la fase di assessment e l’implementazione, è durato dieci mesi (6-7 mesi dall’inizio del progetto vero e proprio), con i seguenti obiettivi: una volta stabiliti i kpi produttivi da monitorare in real time, procedere a digitalizzare il processo di raccolta delle informazioni, quello di raccolta dei dati direttamente dalle macchine, e laddove necessario e conveniente, avviare un percorso di smart manufacturing. «Non ci sono state resistenze da parte dei dipendenti, perché hanno visto la differenza nel modo di lavorare – commenta Silipo -. La rilevazione dei dati in tempo reale, con i sensori installati sui colli di bottiglia di ciascuna macchina, ha agevolato il lavoro di tutti: ha accelerato la raccolta e oggettivato il dato, rendendo più facile e immediata l’identificazione della causa dell’anomalia e la possibilità d’intervento.»
«Ci siamo infatti resi conto che se vuoi ottenere di più dai collaboratori, come l’adesione proattiva al concetto di lean production con una maggiore attenzione agli sprechi di varia natura, devi dotarli degli strumenti necessari per essere più efficaci ed efficienti». In pratica, ora il piano di miglioramento continuo promesso dalla lean è a disposizione di tutti: «Facciamo più cose con la stessa forza lavoro e le facciamo meglio. Tant’è che, grazie alla misurazione oggettiva dell’andamento della produzione, abbiamo appena introdotto, nel contratto di secondo livello approvato con le parti sociali, nuovi parametri per calcolare il premio di produzione, in particolare le non conformità e l’Oee, l’Overall equipment effectiveness, ossia la misura di efficacia totale di un impianto», aggiunge Silipo.
I benefici di breve e medio termine
Il processo di digitalizzazione avviato, con i sensori applicati ai colli di bottiglia scelti come punti di rilevazione dell’Oee per l’intera linea, restituisce i dati di produzione in tempo reale e in forma oggettiva (stato macchina e quantità prodotta). Elimina la raccolta dei moduli cartacei da trascrivere al computer ex post, consente interventi più rapidi di risoluzione, basati su dati effettivi in real time, e crea uno standard di comunicazione del software con il “campo”, cioè le linee di produzione, che favorisce anche l’abitudine a un linguaggio comune tra colleghi e reparti.
Infatti, se il beneficio operativo a breve termine di questo progetto è il supporto tecnologico all’applicazione della lean production, ci sono anche obiettivi organizzativi di medio termine. «Con la redifinizione degli standard lavorativi, si dà concretezza al salto culturale», precisa Mariano di Kpmg. Questi benefici comprendono infatti l’allineamento culturale, oltre che tecnologico, tra le diverse realtà produttive; lo sviluppo di un clima più collaborativo che sostenga il miglioramento continuo; nuove professionalità interne, soprattutto nell’ingegneria di Gruppo nell’It e l’abilitazione di nuove politiche di incentivi all’incremento di produttività, come già previsto nell’ultimo contratto di secondo livello.
«L’obiettivo nel tempo, man mano che cambieremo le macchine e saranno tutte facilmente integrabili fra loro, sarà quello della integrazione completa, con un controllo in remoto dei nostri ingegneri e dell’intera filiera, dai fornitori ai clienti. Siamo convinti che l’automazione non sostituisca completamente le attività umane. Serve invece a eliminare le azioni non a valore aggiunto, aumenta l’efficienza con interventi tempestivi e, da noi, ha già cambiato la dialettica tra caporeparto e manutentore, che ora ragionano con dati alla mano, affidabili e in tempo reale, senza più dare spazio alle interpretazioni letture personali del dato», conclude il direttore delle Operations di Montenegro Paolo Silipo.
interessante