di Ermanno Rondi ♦ Nel passato l’organizzazione era strutturata per reparti con produzioni a lotto economico che ottimizzavano il costo del singolo componente o semilavorato. Oggi l’approccio deve privilegiare il flusso riducendo il più possibile i tempi di attraversamento e il costo complessivo del produrre.

Industry 4.0, Fabbrica intelligente, smart manufacturing, Retail 2.0: sono alcune delle sigle che animano i dibattiti sul futuro del sistema manifatturiero e distributivo. Ciò che lega tutte queste espressioni è l’evoluzione digitale che ormai permea ogni momento della nostra giornata, abituati come siamo con tablet e smartphone ad essere interconnessi con il mondo, dare e ricevere risposte subito a tutti e con tutti. Questa facilità di essere virtualmente ovunque, di verificare ogni cosa, di compararla e di scegliere sulla base delle proprie personali esigenze spinge a modificare profondamente i comportamenti dei consumatori e di conseguenza delle imprese.
A questo modo di pensare indotto dall’interconnessione globale se ne aggiunge un altro motivato da una sensibilità maggiore per gli aspetti green, l’etica delle imprese in senso lato, la percezione del valore dei prodotti e l’esplosione dei servizi ad essi connessi. La reazione delle imprese sposta l’attenzione dal solo prezzo, elemento che ha dominato la fase storica del low-cost e delle delocalizzazioni competitive, ad una strategia d’innovazione e servizio che prevede un presidio molto marcato su clienti e mercati con conseguente prossimità geografica tra produzione e consumo, spinta verso innovazione e customizzazione del prodotto.
È da questi trend che discende l’esigenza di una nuova organizzazione per aziende manifatturiere e distributive. Organizzazione che poi ha un impatto enorme sulla logistica, materia che pratico da trent’anni.
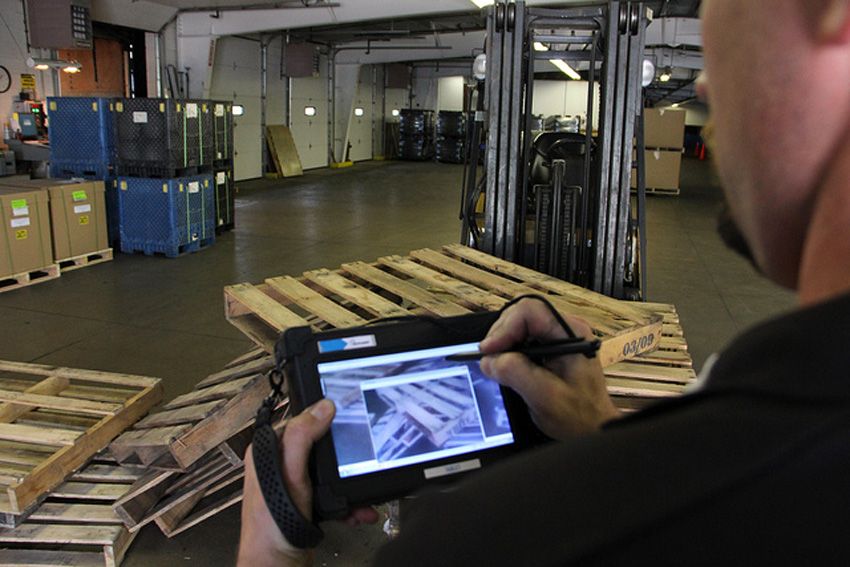
Non confondere tecnologie con strategie. La tecnologia abilita a raggiungere questi obiettivi, ma non è certo il motore principale del cambiamento. È un elemento indispensabile e un abilitatore, ma poi ciò che contano sono le strategie aziendali, i modelli di business. Il dibattito più diffuso è concentrato su elementi tecnologici supportati da sigle ed acronimi, tralasciando spesso le motivazioni ed i benefici per cui si affrontano i cambiamenti sottesi. Le imprese sono in uno stato di sospensione: si intuisce l’importanza di perseguire un percorso di digitalizzazione, ma non sono chiari i benefici attesi. Lo dimostra una recente indagine su Fabbrica 4.0 in cui emergono chiaramente questi contrasti: il 70% degli intervistati prevede forti impatti economici in termini di qualità e flessibilità, ma non ha ancora fatto nulla verso il mondo 4.0; inoltre ritengono, nella stessa percentuale, che la preparazione della propria struttura sia molto bassa, ma nessuno ha pianificato formazione specifica allo scopo. C’è d’altro canto coscienza che non percorrere questa strada significa venire esclusi in tempi rapidi dal mercato. Il vero gap per le imprese non sono gli investimenti, ma la cultura diffusa che questo cambiamento richiede per essere realizzato. L’evoluzione digitale necessita di strutture in grado di comprendere e gestire la tecnologia, ma ancora di più di definire e realizzare i modelli organizzativi che necessariamente prevedono. E’ quindi indispensabile procedere per passi successivi in modo da aggiungere ad ogni step un granello di conoscenza/esperienza e tarando di conseguenza strutture e processi. Se la tecnologia evolve con una rapidità sorprendente, la capacità cognitiva della persona ha tempi e ritmi diversi specialmente se deve innestarsi in comportamenti integrati di squadra.
La Fabbrica 4.0 deve essere davvero intelligente, altrimenti non serve a nulla. Così una Fabbrica 4.0 non può essere ottenuta con un salto decisionale investendo nell’acquisto di una infrastruttura digitale calata dall’alto, ma con un processo che parte dalle esigenze prospettiche del mercato e che evolve per successivi step portando tutta la struttura a rispondere in modo coordinato e consapevole agli stimoli dei clienti. Stimoli che alla fine possono tradursi in pochi e semplici messaggi, ma che si realizzano in obiettivi molto difficili da raggiungere: prodotti personalizzati, consegnati rapidamente, a prezzi molto competitivi, preoccupandosi di tutti il ciclo vita del prodotto.

Da questi concetti nascono anche mestieri nuovi: l’e-commerce ha tassi di reso molto elevati e quindi la re-verse logistic con il carico di controlli, rimessa a nuovo e repackaging è un esempio di attività prima marginali che invece diventano strategiche, la consegna dell’ultimo miglio apre spazi all’ Uber delle cose, esigenze di personalizzazione e vicinanza al cliente inducono l’apertura di microfabbriche nei centri commerciali, l’esigenza di gestire il ciclo vita del prodotto genera nuove attività nell’area manutentiva o di re-manufacturing ed in ultimo il recupero delle materie prime presenti nei prodotti danno origine al de-manufacturing e di conseguenza alla circular economy; produco, riparo, recupero.
Un mondo con nuove opportunità da cogliere. Anche grazie alla tecnologia. Un percorso da affrontare con determinazione, buon senso, sfruttando le tante soluzioni operati-ve che già oggi esistono, affidabili ed affrontabili con investimenti limitati in termini economici, ma significative in termini di cambiamento dei paradigmi organizzativi e culturali. Dai magazzini inter-operazionali integrati con l’avanzamento produzione (manufacturing flow tracking), ai sistemi di prelievo in logica singolo pezzo (single pieces distribution model) fino alla sincronizzazione dell’approntamento ordini con la pianificazione dei mezzi in consegna (delivery plan, track & tracing). Soluzioni diverse, ma un unico comun denominatore: integrare fasi diverse del processo per rispondere meglio e più velocemente al mercato.
Logistica pratica per Industria 4.0
Il tema della logistica è cruciale in un mondo completamente interconnesso. Fabbrica 4.0 e manifattura additiva significano infatti, a tendere, una riduzione dei magazzini al minimo dei minimi e una personalizzazione di massa. Gli ordini vanno evasi in tempo reale e monitorati continuamente. Tutto ciò comporta una totale ristrutturazione dei magazzini e dei sistemi di trasporto. Come fare allora?

L’approccio deve privilegiare il flusso, che deve essere teso. Il primo passo è definire il modello di fabbrica ed un approccio logistico può rappresentare la chiave per iniziare un percorso pratico con passi ben definiti. Nel passato l’organizzazione era strutturata per reparti con produzioni a lotto economico che ottimizzavano il costo del singolo componente o semilavorato; oggi l’approccio deve privilegiare il flusso riducendo il più possibile i tempi di attraversamento ed il costo complessivo del produrre.
Un metodo semplice per descrivere i flussi interni e definire il modello è guardare alla fabbrica come una rete ferroviaria. Questo approccio logistico consente anche di mettere ordine al layout spesso cresciuto sulle esigenze dei singoli reparti e non sull’ottimizzazione dei flussi.
La modellizzazione è semplice:
binari sono i flussi di materiali e possono essere descritti come percorsi che uniscono un’area di polmonatura/deposito ad un punto di lavoro
scambi sono le regole attuative che permettono di scegliere un percorso anziché un altro
stazioni sono i reparti/centri di lavoro/magazzini; tutti i punti in cui si deposita o lavora il prodotto lungo il ciclo produttivo
orari sono l’insieme delle capacità produttive delle singole aree operative
destinazioni è il piano di lavoro definito solitamente dal sistema ERP nella sua veste più ampia e declinato in un Gantt, possibilmente interattivo, a livello operativo
treni sono gli ordini che corrono lungo i binari fermandosi alle stazioni definite dalla destinazione (il prodotto che si vuole ottenere), muovendo gli scambi secondo il percorso necessario alle lavorazioni sottese, cercando di rispettare gli orari
Un modello semplice, facilmente descrivibile che non consente vie di fuga: è necessario descrivere compiutamente l’intero ciclo affinchè funzioni e quindi evidenzia in modo palese ciò che non è ben strutturato o lasciato alle “conoscenze tacite “ dei singoli.
Poiché è necessario abbinare al flusso dei materiali anche il flusso delle informazioni, è indispensabile aver creato un modello di questo tipo: i sistemi ICT non hanno conoscenze tacite. È un modello organizzativo concettualmente semplice che prevede di eseguire in modo controllato e per gradi di automazioni “successive” il percorso verso Industria 4.0.

Su questa base si opera per:
- collegare flussi fisici ed informazioni in tempo reale
- far convergere i dati per ottenere analisi immediate e prendere decisioni on line
- scegliere nuovi percorsi, inserire nuove macchine e/o nuove risorse potendo confrontare e misurare i risultati
- lavorare in termini di servizio verso il cliente
Si può così conoscere in ogni istante cosa succede nel ciclo come se si fosse davanti alla centrale operativa della rete ferroviaria.
Con un modello chiaro e misurabile diventa più facile inserire le tecnologie necessarie; macchine, robot o sistemi più complessi perché sarà sempre chiara la vista d’insieme e le integrazioni necessarie. Continuando nella metafora logistica l’implementazione di questo modello può essere altrettanto semplice. Un sistema di Manufacturing Flow Management System necessita di tre tasselli:
- un modulo di gestione operativa di magazzino (WMS) che possa mappare tutti i polmoni interoperazionali e conoscere la posizione di ciascun componente (materie prime, semilavorati, prodotti ausiliari etc) oltre a definire i percorsi verso i centri di lavoro
- un modulo di controllo avanzamento produzione per poter conoscere lo stato produttivo in ogni istante e quindi gestire le chiamate dei materiali con un flusso teso
- uno schedulatore (Gantt interattivo) per avere chiare priorità e sequenze.
Le logiche Kamban. La strategia produttiva a questo punto può essere basata su logiche Kanban per l’approvvigionamento dei semilavorati e su una logica push sincronizzata tramite il controllo produzione per l’assemblaggio finale.
A questo punto, è doverosa una parentesi per spiegare che cosa sono le logiche Kamban. Si tratta di utilizzare dei “cartellini” come segnali visivi per controllare il flusso di materiali e prodotti. Kanban significa «segnale per fare», o comprare, o muovere, a seconda del tipo. A grandi linee, si distinguono 2 tipi di Kanban:
- kanban produttivo, nel quale il cartellino è il “segnale per produrre”, quindi deve contenere tutte le informazioni necessarie alla produzione (es: linea, dimensione lotto, etc)
- kanban di ripristino materiale, nel quale il cartellino è il “segnale per procurare”, e deve contenere le informazioni necessarie al ripristino (es: nome/codice fornitore, lead time, etc)
L’uso dei Kamban impatta fortemente i sistemi informatici di supporto alla produzione, dove vengono gestite le anagrafiche (materiale, prodotto, fornitore, cliente,etc), la programmazione a medio/lungo termine, i dati finanziari. Ovviamente i sistemi che più devono interfacciarsi con i Kanban sono gli MRP (Materials Requirements Planning) e MRP2 (Materials requirements + Capacity Resources = Manufacturing Resource Planning).
Nella gestione dell’impresa, i 3 macroprocessi che si integrano sono progettazione, produzione e distribuzione. Il Kanban trova il suo utilizzo ideale nel processo produttivo.
Il valore che il Kanban aggiunge è l’informazione immediata, chiara e visibile a tutti di che cosa serve al momento.
Il cambiamento che introduce, rispetto alla produzione tradizionale, è il passaggio dallo “spinto” al “tirato”.
In assenza di segnale, la produzione, o il riordino, avvengono in base ad una programmazione basata sulle previsioni: si produce per ottimizzare la capacità, per “fare volumi”, e si ordina in base all’offerta, spesso in alti volumi perché, a prima vista, più “conveniente”. E’ evidente che le previsioni sono frutto di studi ed analisi accurate, ma rimangono previsioni, cioè non ci dicono cosa esattamente il cliente vuole ora, ma cosa noi pensiamo che vorrà nel medio/lungo termine. La Produzione è quindi “spinta”: la programmazione dice cosa fare, e il magazzino prodotto finito, quando riceve il prodotto, trova lo spazio per stoccarlo.
Vantaggi incredibili per chi adotta questo sistema. Chi ha adottato questa tecnica è passato da 4/5 settimane a 4/5 giorni di tempo di attraversamento riducendo anche i magazzini intermedi. Attivato il sistema è possibile gestire l’introduzione consapevole (simulo, integro e misuro) di qualsiasi grado di automazione: centri di lavorazione che riconoscono il prodotto, robot (collaborative robot), magazzini automatici asserviti alla produzione, moduli CPS (Cyber Physical System) per interconnettere il sistema produttivo in modo flessibile.
L’organizzazione di fabbrica cambia, aumenta l’autonomia delle varie aree operative ed il leader deve avere una visione di insieme: non solo i robot diventano collaborativi, devono esserlo tutte le funzioni aziendali.