
Macchine per il packaging e per il taglio della lamiera, sistemi di illuminazione stradali. Per quanto diversi possano essere i prodotti, i processi e le linee di produzione, il digital twin – di prodotto, di processo e di performance – permette una tangibile riduzione dei tempi di sviluppo e dei relativi costi di progettazione e di processo con conseguente un aumento della produttività. In primo piano le esperienze di Robopac, Prima Industrie e AEC Illuminazione, aziende del top manifatturiero italiano che, in collaborazione con Siemens Digital Industries Software, hanno avviato un percorso d’innovazione. Le soluzioni basate su digital twin e software industriale dell’azienda globale capitanata dal ceo Franco Megali – controllata dalla Digital Industries del colosso tedesco Siemens di cui Giuliano Busetto è l’head della Operating Company in Italia – si sono rivelate strategiche per tradurre i fondamenti della trasformazione digitale 4.0, realizzando concreti vantaggi di efficienza operativa e ispirando nuovi modelli di business basati sulla servitizzazione.
Con il digital twin di processo Robopac ha aumentato la capacità produttiva del 45%, rispondendo in maniera positiva alle criticità sollevate dall’emergenza Covid. Per AEC Illuminazione il digital twin di prodotto ha invece reso possibile lo sviluppo ottimale della produzione di sistemi complessi multifisici – ottici, meccanici ed elettronici – riducendo al tempo stesso i tempi di accettazione delle richieste cliente del 92%. Infine, con il digital twin di processo Prima Industria ha consentito di gestire al meglio le interruzioni di linea, con tempi di risoluzione dei problemi e ripristino delle attività che si sono ridotti da 2 giorni a 2 ore. Il digital twin è un pilastro della fabbrica 4.0, interconnessa e basata sui dati e sulle informazioni da questi estraibili.
Per questo motivo, Siemens Digital Industries Software è diventato pathfinder del Cluster Fabbrica Intelligente, l’associazione guidata da Luca Manuelli (tavolo al quale siedono tutti i portatori di interesse del manifatturiero avanzato, cioè aziende, associazioni, istituzioni, università) che ha il compito di redigere gli scenari tecnologici dei prossimi anni, attraverso un documento, la Roadmap, che poi il decisore politico utilizza o utilizzerà per le politiche industriali e i bandi. Siemens Digital Industries Software darà il suo contribuito alla roadmap per le importanti aree di sua competenza, come è emerso in un webinar (raccontato anche nell’articolo collegato a questo che si può leggere QUI) organizzato in collaborazione col Cluster Fabbrica Intelligente. Le case history raccontate in questo articolo sono state esposte in quel webinar e poi ri-elaborate.
Prima Industrie, il digital twin di performance per una fabbrica “always on”

Prima Industrie è un’azienda storica di Torino che produce macchine laser bi e tridimensionali per il taglio della lamiera con tecnologie di frontiera high-tech. Nata 44 anni fa e quotata alla Borsa di Milano dal 1999 è costituita da 4 business units tra cui Prima Power che si occupa di macchine per lavorazione lamiera, automazione e software. «Il digital twin di performance è stato applicato inizialmente all’interno della nostra produzione per soddisfare i requisiti di virtual commissioning, racconta Ivana Montelli, Software Product Manager di Prima Power. In seguito è stato reso disponibile all’ assistenza dei clienti finali che possono oggi fare affidamento su uno strumento per analizzare e controllare il processo produttivo. Insieme a un partner tedesco che fornisce un CAM tridimensionale di programmazione delle macchine Laser 3d, si riesce a fornire una interfaccia evoluta per controllare completamente il flusso produttivo sia on site che da remoto».
Le soluzioni implementate in Prima Industrie si sono rivelate un potente alleato per creare un valore per il cliente finale, in grado di monitorare e analizzare il processo produttivo. L’obiettivo? Analizzare i dati raccolti da tutte le macchine per incrementare l’efficienza della produzione puntando ad una futura manutenzione predittiva. «Un processo – spiega Montelli – che deve ancora realizzarsi compiutamente e che dovrebbe prevedere lo sviluppo di applicazioni dedicate attraverso la piattaforma cloud IoT MindSphere di Siemens». L’analisi della produzione e la manutenzione predittiva sono alcuni degli aspetti su cui si concentra l’azienda. Tutta la produzione è IoT Ready ovvero le macchine escono dallo stabilimento dotate di gateway che assicurano il trasferimento dati nel cloud Microsoft Azure ed alla piattaforma Mindsphere. Non solo, sulle macchine vengono installate delle videocamere che eseguono un’attività di videosorveglianza. In caso di crash severi si rendono disponibili le registrazioni video per essere analizzate dai tecnici dell’assistenza. I clienti finali ottengono così il supporto per accertare le cause che hanno determinato l’interruzione, offrendo indicazioni sulla possibile risoluzione del problema e ripristinando la produzione il prima possibile.

Insomma, la piena integrazione e condivisione dei dati, permette a Prima Industrie di fornire un’analisi statistica e report esaustivi da consegnare ai clienti. La timeline evidenzia il numero di interventi, il numero di interruzioni e il numero di allarmi. Come racconta Montelli, «Investigando l’occorrenza di questi eventi è possibile avere un insieme di dati che costituiscono la fotografia del sistema nel particolare momento in cui si è verificato il problema». In questo modo Prima Power è nella condizione di avere una conoscenza molto approfondita di quello che succede nel contesto ambientale produttivo. I tools sviluppati da Prima Power permettono una rapida analisi per l’identificazione dei problemi, riuscendo a identificare quali sono le condizioni di machina che possono dare dei disturbi. Tutto ciò ha permesso di raggruppare l’insieme delle possibili cause e, applicando una serie di filtri, individuare delle risposte esaurienti. A fronte di un gruppo di eventi si evidenziano quali possono essere state le cause più importanti (diagnosi) di crash del sistema dando la possibilità di investigare in una certa direzione.
«In passato quando succedeva qualcosa non sempre riuscivamo ad avere sufficienti informazioni. Non si riusciva a capire quali fossero le condizioni dello stato macchina prima dell’evento», aggiunge Montelli. Oggi, l’alto volume dei dati raccolti, opportunamente analizzati nel cloud, abilita un servizio che si rivela fondamentale per risolvere le criticità di produzione che inevitabilmente si verificano nel corso del ciclo vita macchina. Logica che Prima Power applica anche all’intera linea di produzione automatica asservita da robot per il trasferimento dei semilavorati nei vari buffer di parcheggio presenti in linea. Sulla linea sono disposti tutta una serie di sensori per la raccolta di dati macchina – dalla temperatura dei motori ai dati riferibili allo stato di lubrificazione di alcuni utensili. Dati che vengono acquisiti nei diversi stati macchina: run, idle e failure. I benefici del digital twin in Prima Industrie si sostanziano nella riduzione dei downtime migliorando la disponibilità della macchina. I tempi di risoluzione delle interruzioni, quando non intervengono necessità di ricambi, sono passati da giorni a poche ore. Tutto questo ha cambiato radialmente la modalità di assistenza. Le uscite dei tecnici sono oggi piu’ limitate e si riducono ai casi dove l’analisi digitale non produce risposte sufficienti. «Il digital twin è stato un investimento win-win, per noi e per i nostri clienti: ciascuno ne trae un debito vantaggio», dice Montelli. L’azienda prevede un ulteriore di sviluppo evolutivo mirato ad aumentare le performance produttive attraverso tecniche di machine learning che verranno ereditate dalla piattaforma cloud IoT MindSphere di Siemens. Un percorso e una strategia che sono finalizzati a raggiungere una completa manutenzione predittiva.

AEC Illuminazione: il digital twin di prodotto per risolvere la complessità multifisica
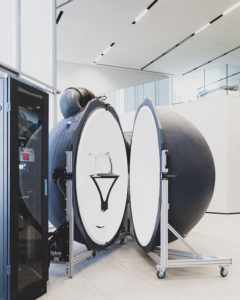
Il caso AEC riguarda l’applicazione del digital twin di prodotto a livello di progettazione e produzione. Il filo conduttore del progetto è l’integrazione del dato in tutte le fasi di processo. Attiva nel settore dell’illuminazione da oltre 60 anni, AEC Illuminazione ha saputo ottenere grande fama a livello internazionale. Milano, Londra, Oslo, Auckland e Dubai, sono solo alcune delle prestigiose città illuminate da AEC. Oggi l’Azienda, con sede produttiva ad Arezzo e presente in 44 paesi, è un importante esempio di eccellenza industriale italiana, conosciuta ed apprezzata in tutto il mondo. Nel suo Headquarters toscano, infatti, AEC progetta e produce interamente apparecchi a LED 100% Made in Italy. Soluzioni per illuminazione di città, tunnel e impianti sportivi con caratteristiche uniche per prestazioni, tecnologia e design. «Essere sui mercati internazionali significa confrontarsi con una competizione elevata, dalla quale ci si può differenziare solo con un miglioramento continuo del prodotto», afferma Tommaso Catalani, Project Manager di AEC Illuminazione.
«I sistemi che realizziamo racchiudono molteplici discipline tecniche, in quanto sono costituiti da componenti ottici, elettronici e meccanici. Tutte queste tecnologie devono interagire nel modo migliore possibile, garantendo il massimo delle performance, facendo fronte alle continue esigenze del mercato costantemente in evoluzione, pur rispettando tutti quelli che sono i requisiti normativi». L’implementazione del digital twin ha richiesto una forte integrazione dei flussi di informazione e dei dati tecnici necessari al ciclo di sviluppo del prodotto. La collaborazione con Siemens si è rivelata decisiva per condividere tutti questi dati attraverso un unico ambiente, permettendone la tracciabilità e l’accesso da parte di tutti i dipartimenti coinvolti nel ciclo di sviluppo prodotto. In questo modo si sono risolte molte criticità nella creazione della distinta di produzione, che in passato, proprio per l’assenza di una vera integrazione tra ufficio tecnico e plant, era fonte di inefficienza. «La simulazione, durante le fasi di R&D e progettazione, è fondamentale per coniugare le esigenze di un prodotto meccatronico alla complessità del design», dice il manager di AEC.

Con il digital twin, ad esempio, si possono misurare le capacità prestazionali in termini termici, che nel caso di apparecchi di illuminazione diventano complessi. Il driver e il gruppo ottico devono garantire determinate funzionalità e performance, mentre la meccanica deve resistere a varie tipologie di sollecitazioni statiche e dinamiche, imposte dalle normative dei mercati internazionali. Riassumendo, centralizzazione dei dati, integrazione multidisciplinare e integrazione software – sia per quanto riguarda la progettazione sia per quanto riguarda la parte gestionale – hanno portato numerosi vantaggi, rendendo più efficienti tutte le fasi di sviluppo e migliorando la comunicazione tra i dipartimenti. Importante è, infine, l’integrazione raggiunta con il CRM, che ha fatto sì che i tempi di gestione delle richieste clienti siano stati ridotti del 92%. L’ulteriore implementazione di configuratori tecnici ha consentito di evadere le richieste in modo automatico nel 90% dei casi. Prossimo passo per AEC sarà la totale condivisione delle informazioni progettuali direttamente da Cad 3D alle macchine utensili e ai processi di manufacturing, migliorando ulteriormente l’efficienza di tutta la filiera realizzativa.

Robopac Smart Factory, con il digital twin di processo capacità produttiva aumentata del 45%

Robopac opera nel packaging, progetta e costruisce soluzioni di fine linea e impianti di confezionamento integrati. La produzione in Italia è organizzata su 7 siti produttivi, tutti nell’area emiliano romagnola. Le soluzioni proposte dall’azienda sono fortemente customizzate e la progettazione consente una elevata configurabilità dei singoli prodotti. Il progetto Robopac Smart Factory è nato nel 2018 con un approccio strategico mirato all’incremento della produttività e al miglioramento della profittabilità ed efficienza dei processi, rendendo il processo produttivo più flessibile sia in merito ai volumi che al mix di prodotti. Dopo un’analisi dell’as is e stabilito il punto di arrivo, to be, rispetto al target definito è scaturito un progetto con due macro aree: da una parte la revisione del layout industriale e dall’altra l’inserimento di tecnologie digital twin nei principali processi di operation. È all’interno di queste due macro aree che si colloca la collaborazione con Siemens.
Le caratteristiche del progetto pilota sono state implementate nello stabilimento che produce macchine semiautomatiche e automatiche di primo livello attraverso cinque linee manuali e una linea automatica. «Lo abbiamo scelto come target del progetto pilota perché vanta una cultura industriale avanzata basata su logiche di lean production, spiega Alessandro Manduchi, Operations Manager di Robopac. Insomma, un sito con standard manifatturieri elevati dove si lavora su un turno al giorno per 5 giorni a settimana, gestendo circa 1.300 ordini di macchine al mese e 120 postazioni di lavoro con un centinaio di operatori impiegati in attività produttive». La soluzione Siemens comprende tre macro moduli: un modulo di schedulazione (upcenter scheduling), un modulo di gestione della attività produttive (la parte mom/mes) e un modulo dedicato alla gestione delle non conformità in produzione. Conseguentemente si sono gestite la gestione degli ordini, la schedulazione e ottimizzazione delle risorse e infine la gestione della qualità. In automatico sono gestiti ordini di produzione, distinte base e cicli di lavoro. La parte di scheduling è rappresentata da un vero e proprio simulatore di linea. Il layout, le postazioni e le risorse sono tutte settate all’interno del software che, andando ad analizzare gli ordini di produzione e le distinte, da un punto di vista dei materiali e cicli di lavoro, genera sequenze di ordini di produzione giornalieri. Il tutto viene traferito al Mes che si incarica di gestire l’esecuzione nelle varie linee. Nel caso di presenza di una non conformità di processo, queste vengono registrate su Mes per poi essere trattate in maniera più specifica e approfondita sull’apposito modulo observer quality.
Tutta la soluzione Siemens è stata poi integrata con gli altri software presenti in azienda, SAP innanzitutto, e il WMS per la gestione di tutti i processi logistici. Nella linea automatica il software di gestione controlla la flotta agv dedicata alla movimentazione dei prodotti lungo tutto il flusso produttivo. Di fatto, è una linea intelligente in cui gli agv e, quindi, gli ordini di produzione vengono trasferiti a opportune aree di lavoro per poi essere reintrodotti sul flusso principale attraverso le informazioni che il Mes è in grado di inviare al controllore degli agv leggendo ordini di produzione e ciclo di lavorazione della macchina. Il flusso si completa con un ritorno delle informazioni da Mes a Sap (consuntivazione tempi, esecuzione e completamento delle varie attività, aggiornamento delle date di produzione e degli ordini). In definitiva la macchina Robopac è tutta completamente automatizzata e integrata. È possibile monitorare in real time lo stato di lavorazione, se la baie soni vuote o in attesa di essere attivate per la produzione, la data di consegna dell’ordine, il modello della macchina e le operazioni del ciclo lavorativo con dati di consuntivo. Le informazioni che arrivano in linea concorrono a definire una serie di indicatori: volumi produttivi, efficienza delle linee di assemblaggio, statistica sui fermi linea e qualità del processo, tempo di consegna e rispetto delle date al cliente oltre ai classici parametri correlati all’OEE. Tutti i dati sono aggiornati in tempo reale con pieno controllo di ciò che succede nel reparto.

Il progetto è iniziato a fine 2018 con tutta l’attività di re-layout dello stabilimento e nel giugno 2019 sono state avviate le attività di implementazione della soluzione che si sono concluse a fine 2020. «Riteniamo che per la vastità e complessità del progetto sia stato un tempo adeguato, dice Manduchi. Cosa abbiamo ottenuto? Ebbene, la capacità produttiva è aumentata del 45% rispondendo in maniera positiva alle criticità sollevate dall’emergenza Covid, effetti che si sono evidenziati soprattutto nel corso di quest’anno. Non solo, siamo in grado di gestire il mix produttivo con maggiore flessibilità grazie ad attività di scheduling e controllo degli ordini e delle risorse. Le info sono disponibili nel plant su più di 70 touch screen. L’operatore, oltre a visualizzare lo stato della lavorazione può visionare la documentazione relativa alla macchina da realizzare, completa di tutti i cicli di lavorazione dei differenti modelli che sono oggi a catalogo. La gestione delle non conformità in linea è diventata più puntuale e di dettaglio: ogni caso viene registrato sul Mes e trattato dall’ambiente specifico».