di Edoardo Calia ♦ Non è solo la replica virtuale dell’ elemento reale nell’ambito dei processi manifatturieri: in quanto elemento abilitante di Industria 4.0, il digital twin è molto di più. Non a caso sta al cuore delle piattaforme di Siemens e Dassault Sistèmes, leader di mercato nel software industriale
L’autore, Edoardo Calia, è Vice Direttore Programmi Strategici dell’ Istituto Superiore Mario Boella (vedi box fondo pagina)
Passare al digitale significa aggiungere ai flussi già esistenti (come materia, energia, denaro) anche un flusso di bit. Potremmo dire così, con riferimento ad esempio al settore manifatturiero, e quindi immaginando di riferirsi al contesto degli stabilimenti produttivi e della organizzazione dei relativi processi.
Dal flusso materiale al flusso digitale
Immaginare che in una catena produttiva esista un flusso di materia è semplice: si tratta delle materie prime o le parti semilavorate che entrano nella linea per essere modificate, rifinite o assemblate. Allo stesso modo è semplice identificare un flusso di energia che viene consumata o prodotta dal processo in esame. Infine, ogni imprenditore ben conosce che a tutto questo è associato anche un flusso economico: lavorare un pezzo ha un costo, la materia prima e i semilavorati hanno un valore quando entrano nella linea, e un altro valore (maggiore) quando ne escono. Immaginare come a questo scenario possa essere aggiunto un flusso di bit può non essere immediato (come è organizzato questo flusso? cosa contiene e cosa rappresenta? dove risiedono i dati digitali che ne fanno parte?).
A queste domande si riesce a rispondere più facilmente se si costruisce il processo di digitalizzazione passando dal concetto di gemello digitale o digital twin,(1) che consiste nel realizzare, per ogni elemento che ricopre un ruolo importante e definito nel processo reale, una “copia digitale” che ha il compito di gestire tutte le informazioni relative al suo gemello fisico (dai dati “anagrafici” fino a quelli generati in real time da sensori di bordo). Una fabbrica digitale si può costruire quindi utilizzando come componenti elementari i gemelli digitali di ogni macchinario (ma anche delle parti da lavorare e dei prodotti finiti): questi saranno connessi tra loro (e interagiranno) con la stessa logica che governa il processo nel mondo fisico.

Non solo una semplice rappresentazione digitale
Il valore che il concetto di digital twin porta nei processi va ben oltre la loro semplice rappresentazione digitale: mediante l’accesso alle copie digitali di macchine, oggetti, materie prime, etc è possibile realizzare applicazioni mirate ad un maggior coinvolgimento di tutti gli stakeholder interessati. Il gemello digitale crea e mantiene la storia del suo gemello fisico: può ricevere informazioni e modificare di conseguenza il proprio comportamento (se si tratta ad esempio di un macchinario), o fornire informazioni sulla evoluzione o stato di avanzamento del processo. Tenendo conto di queste poche – ma intuitive – informazioni diventa più semplice comprendere come sia possibile progettare servizi avanzati della manifattura del futuro quali la fabbrica distribuita e la produzione personalizzata (lot size 1). Ecco, a seguire alcune indicazioni ed esempi utili per la progettazione di un gemello digitale.
Architettura e funzionamento di un gemello digitale
Un gemello digitale è una rappresentazione virtuale (numerica) di un oggetto che ne segue in modo accurato le evoluzioni per una durata temporale che può arrivare a coincidere con il suo intero ciclo di vita (concezione, progetto, costruzione, uso, fino allo smaltimento). La rappresentazione digitale di un oggetto tramite tecniche di modellazione numerica e simulazione non è certo un concetto nuovo: nei decenni passati sono stati sviluppati strumenti informatici più o meno sofisticati che consentono di assistere progettisti e costruttori nelle fasi che vanno dalla ideazione fino alla produzione o assemblaggio.
Questi strumenti normalmente operano in un contesto di pura simulazione (ovvero senza alcuna interazione con la fisicità dei sistemi che essi rappresentano), e anche per questo risultano via via meno efficaci al crescere della complessità del sistema modellato. I modelli numerici presentano limiti anche nelle situazioni nelle quali si intende osservare (simulandoli) comportamenti che si articolano su un arco temporale ampio, nel quale intervengono – nel mondo reale – fenomeni complessi che possono avere un impatto importante sulle prestazioni, quali usura di parti meccaniche o degli utensili. La qualità della simulazione di fenomeni complessi può essere significativamente migliorata se alle grandezze stimate dal modello numerico si affiancano dati provenienti da misure effettuate nel mondo fisico, sull’oggetto reale.
Possiamo quindi dare una definizione più accurata di digital twin, affermando che si tratta del modello numerico di un oggetto al quale siano aggiunte funzionalità di scambio di dati con il suo corrispondente nel mondo fisico e che ne segue le evoluzioni nel tempo mantenendone aggiornata la rappresentazione virtuale.

Il gemello digitale e il suo ecosistema
Partendo da questa definizione relativamente generica è possibile identificare alcuni requisiti essenziali per gli oggetti fisici dei quali si desidera realizzare un gemello digitale, nonché alcune funzionalità necessarie per il sistema informativo preposto alla gestione delle loro rappresentazioni virtuali. È importante osservare che, sebbene il contesto al quale si fa riferimento nel seguito è quello della manifattura (quello nel quale il concetto stesso di digital twin ha avuto origine), le considerazioni fatte si possono applicare a qualsiasi processo di digitalizzazione.
Connettività di rete, sensori, attuatori
Dal punto di vista del sistema che si intende complementare con la sua copia virtuale, sono fondamentali la connettività di rete e la dotazione di dispositivi di misura e/o attuazione: sensori che consentono la misura di selezionate grandezze fisiche da inviare periodicamente al gemello digitale, e attuatori che mettono il gemello digitale in condizioni di poter inviare dati che possano essere tradotte in azioni nel mondo fisico (2).
Data mining e machine learning
Per quanto riguarda il sistema informativo che supporta la implementazione del gemello digitale, esso deve fornire funzionalità di archiviazione di grandi moli di dati e sofisticate capacità di elaborazione, utilizzando tecniche avanzate di data mining e machine learning.
L’architettura di comunicazione
Il terzo componente del puzzle della digitalizzazione è la comunicazione tra l’oggetto fisico e il suo gemello digitale, la quale deve avvenire nel modo più efficace e in linea con i requisiti: deve pertanto essere definita con precisione la architettura di comunicazione in termini di protocolli di rete e interfacce HW e SW.
Dettagli ulteriori, incluse le scelte tecnologiche e architetturali per il sistema informativo e per le modalità di comunicazione, possono essere definiti solo analizzando il caso specifico di interesse.Nella sezione seguente viene proposto un approfondimento in tal senso per il caso specifico della digitalizzazione della manifattura.
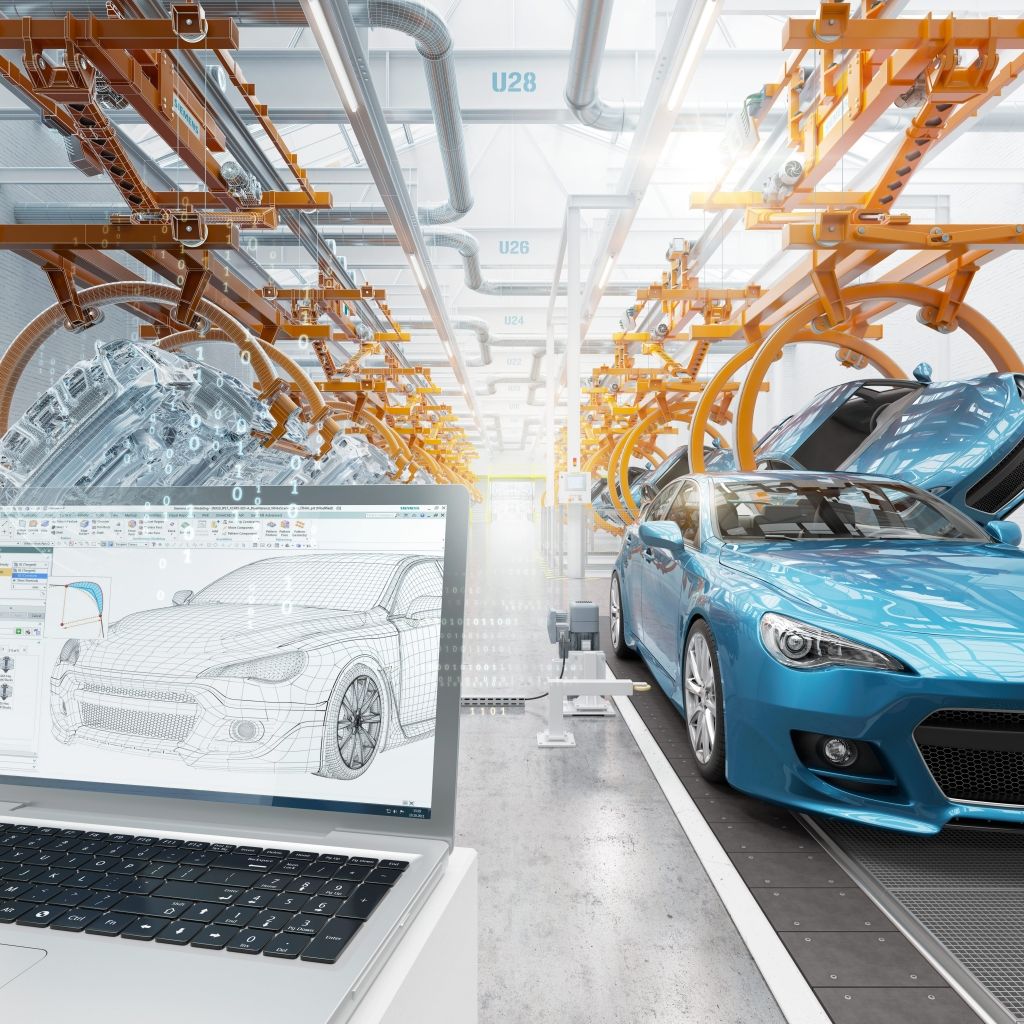
Il digital twin nei processi della manifattura
Il settore della manifattura, che come già osservato sta vivendo una fase di forte spinta verso la digitalizzazione, può trarre significativi benefici dalla introduzione del concetto di digital twin, proprio perché presenta molte delle complessità citate nella sezione precedente che non possono essere affrontate in modo soddisfacente utilizzando tecniche di semplice modellazione numerica. I protagonisti del processo manifatturiero sono sostanzialmente aggregabili in due categorie: i macchinari che eseguono le lavorazioni e gli oggetti o componenti che vengono da esse trasformati. Utilizzando i digital twin la digitalizzazione del processo manifatturiero può essere affrontata con un approccio modulare, pianificandola in modo graduale.
La progettazione del digital twin di una macchina utensile deve rispondere ai criteri generali già citati, che possono essere dettagliati per il caso specifico come segue:
La modalità di connessione in rete della macchina
Questa dipende dal fatto che questa sia o meno predisposta per scambiare dati con il mondo esterno. Le macchine di ultima generazione presentano componenti HW e SW che consentono la comunicazione con il mondo esterno, mentre quelle di vecchia generazione – ancora ampiamente utilizzati negli stabilimenti produttivi – non sono equipaggiate in tal senso. L’adeguamento ai canoni tipici della Industry 4.0 può essere ottenuto anche per queste attrezzature aggiungendo sensori e moduli di elaborazione (sistemi embedded) in grado di rilevare e trasmettere le grandezze di interesse (tecnica detta refitting, che deve essere messa in atto senza interferire con l’elettronica di controllo eventualmente già presente)
Il sistema informativo che ospita il digital twin
Deve avere come componente fondamentale una base dati progettata per gestire informazioni molto eterogenee, che possono andare dalla anagrafica del macchinario (informazioni statiche, immutabili nel tempo quali data di acquisto, costo, produttore, modello etc), allo storico delle operazione di manutenzione (variabilità relativamente lenta), fino ai dati raccolti in near-real-time dai sensori di bordo, flussi molto più significativi dei precedenti che generano un volume di dati molto maggiore. Alla struttura preposta alla gestione dei dati sono affiancati uno o più moduli SW che costituiscono l’intelligenza del digital twin. Questi possono includere strumenti di simulazione (della macchina) e algoritmi sofisticati i quali, potendo agire su informazioni misurate nel mondo fisico oltre a quelle stimate, sono in grado di fornire risultati e informazioni estremamente accurati.
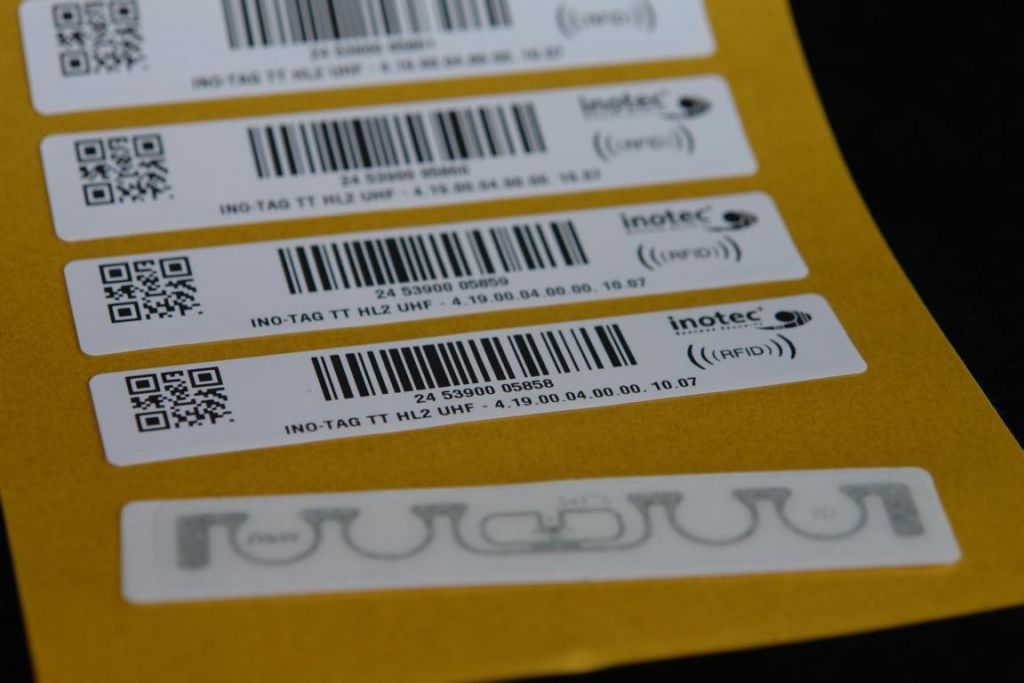
I digital twin dei prodotti realizzati o dei pezzi in lavorazione
Per completare la digitalizzazione del processo di manifattura occorre predisporre anche i digital twin dei prodotti realizzati o dei pezzi in lavorazione, creando nel sistema informativo una copia digitale di ciascuna delle parti che attraversano la catena di lavorazione (che potrebbe ad esempio essere creata all’atto dell’ordine). La comunicazione tra gemello fisico e digitale nel caso delle parti in lavorazione è necessariamente molto semplificata rispetto al caso delle macchine utensili: è sufficiente ad esempio che i pezzi in lavorazione siano riconosciuti dai macchinari (usando lettori di codice a barre o RFID), abilitando così servizi di lavorazione personalizzata (mass personalization) e tracciabilità del singolo componente. Il gemello digitale del prodotto contiene infatti informazioni sulle specifiche richieste avanzate dal cliente in termini di materiali, colori, finiture, dimensioni. Quando il pezzo da lavorare viene identificato dalla macchina utensile, il digital twin della macchina può dialogare con il digital twin del pezzo per ottenere informazioni sulla specifica lavorazione da eseguire.
Il punto di arrivo: la digitalizzazione completa del processo produttivo
Immaginando di replicare nel mondo virtuale dei digital twin le stesse connessioni e interazioni che esistono nel mondo reale, si ottiene la digitalizzazione completa del processo produttivo, che rende possibili in modo automatico numerosi servizi di grande valore per imprenditori, manutentori, e operatori delle macchine: l’utente interessato – e autorizzato – ad avere informazioni puntuali sull’avanzamento dei processi o sugli eventi che si verificano può ottenerle facilmente interrogando i gemelli digitali dei macchinari o degli oggetti interessati.
Oltre la manifattura, fino allo smaltimento
A conclusione di questa semplice introduzione al concetto del gemello digitale e al suo utilizzo negli stabilimenti produttivi, è importante osservare che concettualmente il digital twin di un prodotto continua a seguire il suo gemello fisico anche dopo che questo lascia la fase di manifattura, entrando quindi nella fase di uso vero e proprio. Per tutta la parte rimanente del ciclo di vita del prodotto il digital twin può continuare a ricevere e memorizzare informazioni sul suo utilizzo, la sua localizzazione, il suo stato di funzionamento e usura. Un insieme di dati di grande valore – ad esempio – per il produttore, che interrogando i digital twin dei propri prodotti può ricavare informazioni utili per migliorare il servizio ai propri clienti.
Il numero e la tipologia dei servizi che si possono offrire utilizzando i dati memorizzati nei gemelli digitali è limitato solo dalla fantasia: dal marketing dei prodotti alla manutenzione preventiva di strumenti e macchinari, dalla formazione alla pianificazione avanzata e ottimizzazione della produzione, fino alla decentralizzazione della produzione. Questi e molti altri sono gli elementi caratterizzanti dell’industria del futuro, quella che sta emergendo a grandi passi da quella che qualcuno ormai chiama la quarta rivoluzione industriale.
[boxinizio]
L’Istituto Superiore Mario Boella
L’Istituto Superiore Mario Boella (ISMB), del quale l’autore di questo articolo, Edoardo Calia, è Vice Direttore Programmi Strategici, è un centro di ricerca applicata e di innovazione focalizzato sulle Tecnologie dell’Informazione e della Comunicazione (ICT). Fondato nel 2000 da Compagnia di San Paolo e Politecnico di Torino, oggi l’Istituto si avvale delle competenze tecnologiche e di processo di circa 150 ricercatori che lavorano in stretta collaborazione con l’impresa, l’accademia e la pubblica amministrazione. Presieduto da Andrea Alunni, con direttore Massimo Marcarini, l ’Istituto opera secondo il modello della gestione della conoscenza, intervenendo non solo nella creazione dell’innovazione, ma seguendone anche la fase implementativa e la successiva evoluzione. Questo approccio – che recepisce le linee evolutive della ricerca europea – rappresenta un passo in avanti rispetto al mero trasferimento tecnologico.
ISMB, situato all’interno della Cittadella Politecnica, il nuovo polo di espansione dell’attività didattica, di ricerca e di trasferimento tecnologico del Politecnico di Torino è organizzato in Aree di Ricerca orientate ad alcuni dei principali ambiti dell’ICT: infrastrutture di calcolo basate sul cloud computing e simulazione elettromagnetica (Advanced Computing & Electromagnetics), telecomunicazioni ottiche e optoelettronica (Applied Photonics), uso delle tecnologie dell’informazione e della comunicazione a supporto dello sviluppo sostenibile (Innovation Development), applicazioni per dispositivi mobili e data management (Mobile Solutions), sistemi wireless per l’erogazione di nuovi servizi su canale mobile (Multi-Layer Wireless Solutions), tecnologie e applicazioni per la navigazione satellitare (Navigation Technologies), sensoristica wireless e sistemi abilitanti l’Internet of Things (Pervasive Technologies).
Nel 2011 l’Istituto ha esteso il proprio campo d’azione all’innovazione di processo, con particolare attenzione ai temi prioritari dell’agenda europea. Questa evoluzione intende valorizzare le eccellenze tecnologiche e i risultati conseguiti dalle Aree di Ricerca nell’ambito dei Programmi Strategici (Smart Energy, Smart City e Smart Health) che, per loro natura, necessitano di competenze trasversali. Sempre in un’ottica di innovazione di processo, ISMB ha sviluppato una forte competenza nell’analisi di nuovi modelli di business che costituiscono una componente fondamentale per garantire la sostenibilità delle soluzioni innovative. L’Istituto è inoltre impegnato in varie collaborazioni industriali con imprese grandi e medio-piccole, oltre che in iniziative di alta formazione di respiro internazionale realizzate in stretta cooperazione con l’accademia.
Nel luglio 2013 la struttura organizzativa di ISMB è stata ulteriormente aggiornata con l’intento di perseguire tre obiettivi primari: consolidare le attività delle Aree di Ricerca attraverso l’accorpamento e la focalizzazione delle competenze; continuare a sviluppare i Programmi Strategici; migliorare e valorizzare i rapporti con gli stakeholder, sia internamente che esternamente all’Istituto, grazie alle Funzioni. Queste ultime svolgono attività di supporto alle Aree di Ricerca e ai Programmi Strategici, curando il presidio delle tendenze e delle opportunità di ricerca emergenti (Emerging Trends & Opportunities), l’elaborazione di modelli innovativi di formazione post-universitaria e professionale in grado di valorizzare le competenze tecnologiche di ISMB (Higher & Professional Education), il supporto nella diffusione delle attività di ricerca e dei risultati conseguiti dalle Aree e dai Programmi (Front-End, Marketing & Communications) e il coordinamento dei processi istituzionali (Research Support & Secretariat).
[boxfine]
Note:
1) Nella sua forma più semplice il digital twin è un contenitore virtuale di dati atto a raccogliere e memorizzare informazioni sul ciclo di vita del corrispondente oggetto fisico. È tuttavia importante notare che esso può essere complicato a piacere, fino a rappresentare un vero e proprio modello dell’oggetto, in grado di simularne il comportamento a diversi livelli di dettaglio.
2) La connessione bidirezionale dei macchinari in rete è uno dei prerequisiti per poter accedere alle agevolazioni previste dalla attuale normativa italiana in materia di evoluzione verso Industry4.0